Lettre d'information "The Sharp-E"
Juillet 2018
En tant que fabricant, il est impératif de vous assurer que la géométrie de vos outils est en parfait respect de vos définitions afin de garantir des performances de coupe supérieures. En respectant cela, vous prenez l’avantage sur vos concurrents et vous contribuez à la construction de votre réputation. En tenant compte de cela et, des progrès technologiques sur le marché, on s'attend à ce qu'un outil fini soit précis jusqu'au dernier micron.
Thomson Mathew, Chef produit logiciels déclare : «Nous travaillons en étroite collaboration avec Zoller depuis de très nombreuses années pour que leur machine de mesure et nos logiciels communiquent facilement entre eux afin de simplifier et d’améliorer la mesure des outils, la mesure des meules et le processus de compensation. Ce partenariat offre des avantages majeurs à nos clients en automatisant et en affinant le processus de mesure des outils.»
« La méthode traditionnelle pour la mesure d'outil nécessite de tailler un outil, puis de prendre manuellement cet outil pour le monter sur une machine de mesure indépendante ; on mesure alors des paramètres tels que l'hélice, le diamètre extérieur et l'angle de coupe, puis on procède à la phase de compensation pour respecter les paramètres de conception. Faire cela manuellement est risqué car il peut y avoir des erreurs de données causant au minimum des rebuts.»
« ANCA s'est associée à Zoller pour construire l'infrastructure et les systèmes partagés permettant une communication automatique entre la machine à mesurer Zoller et la machine de taillage ANCA, éliminant ainsi toute introduction manuelle. J'ai travaillé avec nos clients pour mieux comprendre les enjeux de l’organisation des ateliers de fabrication, l’automatisation du process de taillage et l’obtention de rendements significatifs, d’outils de meilleure qualité et moins de pièces rebutées. »
« Cela nécessite d’être très précis et de s’assurer que nous connaissons intimement le produit de l’autre et vice versa ; ainsi l’usine de production et de recherche Zoller en Allemagne possède la dernière version logiciel ToolRoom et du logiciel de simulation et nous avons la dernière version logiciel et matériel chez nous pour nous assurer que nos développements respectifs fonctionneront bien ensemble.»
« Des interfaces spéciales ont été développées pour la communication, comme le logiciel Measurement Machine Wizard qui est automatiquement mis à jour d’un côté comme de l’autre chaque fois qu'il y a une exigence de mesure et de compensation. Les données peuvent être transférées via le réseau informatique de l'atelier si la machine ANCA et Zoller sont sur le même réseau ou via une clé USB. "
«Nous aurons le Zoller Genius III sur notre stand à IMTS, stand 237406, Bâtiment Nord, Niveau 3 et nous en avons souvent un dans nos différentes salles de démonstration dans le monde. Renseignez-vous auprès de votre représentant local et découvrez les bénéfices de ce partenariat », a conclu M. Thomson.»
Les trois fonctionnalités principales qui améliorent la qualité de l'outil et le processus de fabrication:
Mesure automatique des meules
Pour gagner du temps de production, les clients mesurent souvent les trains de meules sur des bancs externes et conservent ces informations sur les machines lorsque les types d'outils sont modifiés. Pour obtenir des mesures très précises et éliminer ces processus manuels, tous les trains de meules des machines ANCA sont compatibles avec les adaptateurs Zoller pour permettre le transfert direct des données depuis notre éditeur de meules vers Zoller et vice versa. Les données de mesure de la meule peuvent être automatiquement transférées vers une machine ANCA ou un logiciel de simulation.
Mesure automatique des paramètres de conception et compensation
Pour la production en grande série, il est nécessaire de valider les paramètres du premier outil. S'il y a des variations dans la géométrie, alors des corrections doivent être faites avant de procéder à la production.
Zoller et ANCA ont conçu conjointement une interface utilisateur graphique (GUI) pour transférer directement les données de l’affûteuse vers la machine de mesure Zoller via le réseau ou une clé USB. Les capacités logicielles sont disponibles sur les deux systèmes pour ensuite pouvoir sélectionner les corrections requises sur les paramètres des outils et que la production soit lancée.
Logiciel pour la numérisation et la correction automatisées des contour d'outil
Les outils de profils complexes comme les fraises « sapin » ont des tolérances très serrées ; le pas et formes ont besoins d’être corrigés suivant les erreurs des meules. Après la fabrication de l'outil, son contour est automatiquement scanné grâce à la fonction Lasso de Zoller. Lasso exécute une comparaison nominale / réelle entre le contour balayé et le contour tel que défini dans le fichier DXF. Zoller calcule également automatiquement un contour corrigé basé sur cette comparaison nominale / réelle et le transmet au logiciel ANCA ToolRoom qui prend la nouvelle forme corrigée pour le prochain taillage.
Les paramètres suivants peuvent être mesurés et communiqués entre iGrind et Zoller Genius III.
Sur la longueur taillée de l'outil :
• Longueur OD
• Diamètre
• Angle de chanfrein
• Largeur de la zone de chanfrein
• Longueur du chanfrein (mesurée en X le long de l'axe de l'outil)
• Rayon d'angle
• Angle de l'hélice
• Angle de coupe goujure
• Angle en bout pour les fraises à bouts droits ou à rayon en bout
• Angle de dépouille OD (primaire, secondaire, tertiaire)
• Largeur de dépouille OD (primaire, secondaire)
• Largeur radiale
• Angle de dégagement en bout (primaire, secondaire, tertiaire)
• Largeur de la surface de l'extrémité (primaire, secondaire)
• Plat en bout
• Angle de pointe
• Diamètre du noyau / profondeur de goujure
• Conicité OD
• Diamètre de dégagement OD
• Angle d’ouverture
• Multi-drill Rayon S
Qualification des meules
• Diamètre
• Rayon tore
• Distance à la face avant et arrière (largeur implicite)
• Angle de chanfrein
• Position arête pour double chanfrein
Compensation de profils
• Hémisphérique
• Rayon en bout
• Profil
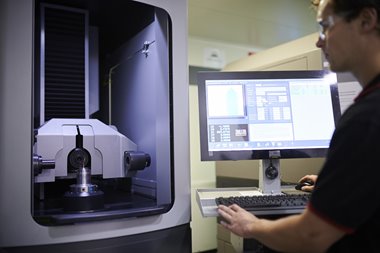
17 juillet 2018