E-Sharp News
March 2020
ANCA’s ToolRoom RN34 is the right tool for the aerospace, die mould, general machining and power generation industries - offering improved productivity through the intuitive creation of complex endmill geometries.
The transition from combustion engines to electric vehicles in recent years has seen a slow decline in the demand for cutting tools in the automobile industry. As this trend continues, cutting tool manufactures are looking for alternate market segments to maintain the supply of cutting tools and stay competitive and profitable. ANCA’s ToolRoom RN34 was released to market in September 2019 with advanced features and complex geometries; and has come at the right time for our customers to diversify and venture into other market segments.
ToolRoom RN34 comes with a suite of features focusing on the aerospace, die mould, general machining and power generation industries, offering improved productivity and intuitive creation of complex endmill geometries .The CAGR (compound annual growth rate) for next 3 years for the four industries combined is predicted to be 22.3% of the global cutting tool consumption*. ToolRoom RN34 has made the design and manufacturing of high-performance endmills a real possibility for the above industries.
ToolRoom’s enhanced features and grinding solutions are driving increasing demand for the RN34 release, as customers race to be the first to manufacture and supply these high-performance tools to capture market share.
Tool Balancing
Chatter is the enemy of high-quality surface finish, dimensional accuracy, and tool and machinery life. Tactics to minimise this include the work holding, controlling feeds and speeds, and (most importantly) tool design. The ability to design and manufacture variable helix/lead and pitch to avoid chatter has been a long-standing software offering. Variable helix/lead with angle changes along the flute have also been used. These options can change the angle and the timing with which the workpiece is engaged and eliminate harmonics.
However, variable helix/pitch introduces uneven weight distribution throughout the tool and will need balancing at higher RPMs. Balanced tools can push up speeds, feeds, depth of cut and eliminate the likelihood of unwanted vibrations and chatter. In the past deploying any or a combination of these techniques has involved a lot of trial and error among toolmakers, highlighting the blend of art and engineering involved.
The high complexity of such endmills designed to minimise chatter has influenced the development of Tool Balancing in the ToolRoom RN34 release and has been in high demand. Customers and end-users are extremely happy with the performance of balanced tools especially in the die mould, power generation and aerospace industries. “Direct communication between design and simulation software packages has simplified tool balancing and made it a breeze,” says Thomson Mathew, Software Product Manager.

“With ANCA’s balancing software we have a tool balanced generally within five minutes. Some of our more complex tooling can take a little longer – up to 20 minutes. This drastically decreased our time in setup on the machine which could take several hours. Our biggest success story has been an aerospace customer who is running our 1” aluminum roughing tool at 25k rpm. We also have another large prototype customer machining aluminum molds and we balance every tool for them. This has allowed us to get better surface finishes on their parts compared to their previous tool supplier.”
Douglas Franke, Fraisa Production Manager
Designer cutting edge
The constant helix ballnose option has been replaced by a graphical drag-and-drop designer cutting edge. This ballnose type of tool, with optimised irregular helix curves to reduce vibration, and with near-instant visualisation is easily achieved by switching from the 2D projection of the cutting edge to the 3D. These tools are also increasingly popular in the die mould, power generation and aerospace industries.
Ballnose tools with low helix along the ball are generally used for the finishing of hard materials and the high helix for aggressive cutting since it improves fracture resistance and the optimised curve reduces vibration.

Designer Edge

Machining of core for die mould sector

Machining a blade
Ballnose chisel grinding feature
Grinding a standard ballnose cutting tool with the correct chisel angle, straightness, the correct chisel relief and achieving the correct line form for the ball profile is not an easy task. It’s even more difficult when it’s the designer cutting edge; but ToolRoom RN34 has made this an easy task by automating the entire process. The end-user only needs to choose the style of chisel with the required angle based on the application and the new cycles populate the grinding parameters automatically. This enables centre cutting of ballnose tools and eliminates wear and tear of the tip section.
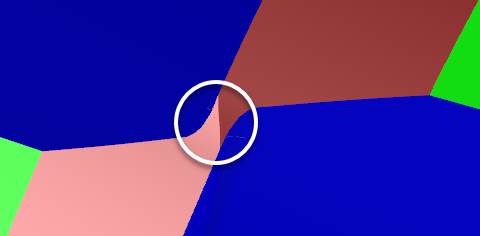
Chisel edge with web thickness
Other features within the latest version of ToolRoom RN34 include revamped ToolTypes. These include double radius endmills, threadmills, lollipop cutters, countersink tools, pocket grinding applications, embedded grinding files, new grinding methods, chip breaker operations, constant helix fir tree cutters, protection for grinding files, double margin drills, and various other enhancements in profile software and other ToolTypes.
ToolRoom RN34 is a complete package focused on enabling end-users to design and manufacture a wide range of complex tool geometries. Don’t be afraid of changing technologies but think about how they can be leveraged to create new levels of productivity,” concludes Thomson Mathew.
------------------------------------------------------
* Dedalus Consulting 2019,
Cutting Tools Global Market Analysis 2019, Global Markets by Products, End-Users, Applications and Competition: 2019-2025 Analysis Forecast, Dedalus Consulting, New York, viewed 06 February 2020<
https://www.dedalusconsulting.com/index.php/industries-covered/machining-materials-series/cutting-tools-menu/cutting-tools-world-market>
13 March 2020