E-Sharp News
July 2024
Founded 50 years ago as Carbide Grinding Company in Waukesha, Wisconsin, you could say the firm really shook the jungle when second generation owner Kevin Cranker introduced the variable helix, variable index, Gorilla Mill in 2005. The tool was such a hit that the whole company has taken its name, and they’ve been howling about it ever since.
Gorilla Mill is now a three-shift operation in a thoroughly modern 24,000 sq. ft. facility, with dozens of 5-axis tool grinders, a full blank prep department, sophisticated QC equipment, and centralized coolant filtration and mist extraction (with all utility lines running in trenches underneath the production floor). But how could they make such a revolutionary tool back in 2005?
The answer, says third generation Operations Manager Nathan Cranker, was ANCA. “In a lot of ways, it was thanks to ANCA that we were able to develop the Gorilla Mill. Because even back on our RGX and TG7 machines, which are ancient, their software had the capability to manufacture the parts we dreamt up.”
Cranker also points to ANCA’s frequent upgrades to the software, “so that we can make tools faster, which is invaluable. I really appreciate them for the work they do on that.” What’s more, he adds, “when we found ANCA, it just stuck immediately. The software was very user friendly, so we were able to understand it quickly.” Conversely, “to this day, other machine manufacturers still struggle to make a Gorilla Mill.” There are other end mills on the market with similar features, but the Gorilla Mill’s geometry is patented and remains a challenge for other grinders, says Cranker.

Holding microns with ease
With a few frustrating exceptions, since they first switched to CNC, Gorilla Mill has built their business on ANCA machines. And they’ve embraced new ANCA technology as it comes. Their new MX7 Ultra is the latest such example.
Gorilla Mill already had a stable of MX7 Linear machines, which continue to perform well. So why the Ultra? “We have aerospace customers who demand plus zero and minus five ten-thousandths of an inch on the diameter and end form on ball nose tools,” Cranker reports. “And the tolerances are getting tighter…It seems the MX7 Ultra was designed for situations like this. [Tools] fluctuate maybe a tenth or two here or there, and only over a long period of time. It’s a game changer. And the guys on the shop floor absolutely love it.”
How is the MX7 Ultra able to hold such tight tolerances over long production runs without operator intervention? First, explains Cranker, the machine’s control resolution is one nanometer, which is 10 to 100 times finer than competing machines (including the MX7 Linear). Another bit of magic is the new control algorithm, which capitalizes on the improved control resolution to move through contours with greater speed and almost perfect precision. The Ultra also has Motor Temperature Control (MTC), a patented system that varies the current to the motor, rather than relying on liquid run through a chiller, to keep the spindle to within 0.5°C. This minimizes spindle growth even as grinding conditions change.
“The original MX7 is a fantastic machine, but—and I don’t say this in any way to throw a negative light—it requires a little more hands on maintenance from the operators to make tight tolerance tools in high volume,” observes Cranker. “They’d have to check the machine more frequently. But we were able to throw these tough, tight tolerance jobs right on the new Ultra and a lot of our problems went away. It’s producing tools more consistently, whether it be to the tolerance, or just overall from job to job. ANCA has come out with a next level product that has made it even easier for us.”

Real-time compensation
It should be noted that ANCA offers options for improving grinding precision on all their models, features that Gorilla Mill has taken full advantage of. For example, automatic runout compensation uses the standard Renishaw probe to check the tool blank in 3 planes, digitizes the actual centerline of the tool, and then compensates the entire machine kinematic to grind relative to that center, rather than the centerline of the work head. The resulting grind is nearly flawless. And the feature adds just 25 seconds in cycle time.
ANCA also offers an internal non-contact tool measuring system called LaserUltra, which uses a Blum DIGILOG laser to perform either digital or analog scans of a tool profile. LaserUltra can scan an entire tool profile in about 10 to 12 seconds, compare the measured profile to the nominal, and within roughly 5 seconds, automatically adjust either the wheel file or the grinding program (as required), to bring the tool to within specifications. Cranker says that on an Ultra machine, such systems enable Gorilla Mill to grind ball nose end mills all night in an unmanned shift to within 0.0001” (±2 microns).
As smooth as a baby gorilla’s behind
Cranker also recounts that when ANCA introduced linear motors to their MX line of machines, it made an immediate improvement in surface finishes. Tools ground with a standard 320 grit wheel suddenly appeared as if they were ground with a 400 grit wheel (for example). He says the higher resolution of the Ultra machine has made yet another improvement, such that a 320 grit wheels perform as if it’s a 600 grit.
“It’s huge. Considered at the micro level, the machine’s smoothness really lets the wheels do what they need to do. It makes the finish even better, like a mirror, with very little effort. That’s what I really like about that machine.”
Cranker credits this capability with giving them another competitive advantage in the marketplace. “Not only that, but it also provides peace of mind. A lot of customers have strict demands for the highest end tooling. When we show them their tooling is going on these state-of-the-art machines, they absolutely love it.”
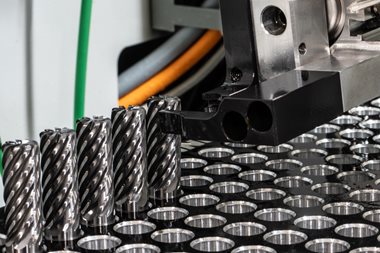
Blank prep upgrade
Like many tool manufacturers in the 2000s, Gorilla Mill relied on TRU TECH machines for OD blank grinding. But when ANCA introduced the CPX Linear pinch peel grinder in 2018, Gorilla Mill jumped at it and “we haven’t looked back since,” says Cranker. “The key factor—and it’s one of the main things we love about ANCAs in general—is that they get production shops like us. Their years of knowledge on loader systems and automation really shows in the CPX.”
Like the MX7 Ultra, the CPX Linear has both linear motors and MTC. The roughing spindle boasts 43 kW (58 HP) for high throughput. A rigid steadyrest bolted into the polymer concrete base helps deliver micron level precision. Cranker also praises ANCA’s approach to the software. “They didn’t compromise and try to make their original tool grinding software work for OD. You could tell they started from the bottom up, and really made good, usable software. I feel confident that any of the operators running our cutter grinders could run the CPXs with a week of training. It’s that kind of plug and play.”

What’s next?
With the bold motto “world domination,” Gorilla Mill is driven to pursue continued growth. To do that, says Cranker, they aim to expand their drill lines and boost sales with other new products, like thread mills, which they introduced five years ago, and chamfer mills, just a year ago.
They also plan to push technology in things like coatings. For example, Cranker says, their proprietary GMS2 PVD coating is an improvement on the original Gorilla Mill options, such that they dubbed the end mills with GMS2 the Super Bitchin’ line. But that’s now been surpassed by their new WTF coating. “This one’s a real game changer,” reports Cranker. “It’s on some of our highest performance tools and people have been seeing a lot of success with it. It can eat high temperature alloys like nothing. It wants to be run hard.”
Gorilla Mill clearly isn’t shy. As Cranker puts it, “we’re not the guys with a white tablecloth booth at IMTS. We’re the guys getting noise complaints, and it’s worked really well for us. We like making a ruckus and we have fun with what we do. Business is business, but you’ve got to love what you do, and that’s what we embrace here.”
Their embrace of ANCA seems sure to continue, as Cranker describes the relationship with ANCA as a “perfect match. Their automation capabilities are second to none, as far as I’m concerned. And that’s really helped us grow.” Likewise, he praises ANCA’s ability to deliver machines when needed. “We’ve got to work with a company that’s as nimble as we are.
“It’s been great to watch ANCA grow with us. And it seems to me that they’ve pulled out ahead of other builders. The equipment they’re making, the progress they’re making…they’re leaving people in the dust.”
19 June 2024