电 子 简 讯
2011年12月
通常,砂轮的全部潜力并未得到充分利用。这可能是因为缺乏系统方法的缘故。以下说明的一种系统方法,有助于建立磨削程序的有效主要参数。
这种方法既可以应用于普通的缓进给磨削工序,也可以应用于铣刀和丝锥的凹槽磨削工序;既可以使用普通磨料,也可以使用超硬磨料。
建议采用的方法,分为六个程序步骤。我们用一些简单公式来定义一些主要参数。
程序步骤:
- 目的
- 准备
- 运行
- 评估
- 记录
- 发布
目标
首先,明确想要实现的目标。有些目标可能相互冲突,如既想提高切除率,同时又想取得更佳程序稳定性。其中一些目标可能包括:
- 修正现有问题(烧伤、表面精度、尺寸稳定性)
- 改善加工经济性,如延长砂轮使用寿命
- 提高材料切除率,即缩短加工时间
- 测试新的规格
- 提高磨削生产结果的稳定性
准备
如果任务是现有程序,则要熟悉主要问题并做好记录。其中包括:
- 材料切除率 Q’w 或 Q-prime (记住Q’w = (vw x ae)/60 = (进给率 vw (单位:毫米/分钟) x 磨削深度 ae (单位:毫米), 除以60)
- 砂轮速率比 vc
- 进给率 vw
- 磨削余量总量和磨削深度 ae 以及磨削数目
- 检查喷嘴是否受损,确定并记录喷嘴位置
- 测量冷却液温度(早晚)并检查流量
- 修整速率比 qs、进给量、同步或异步修整
- 在磨削周期期间检查电流计记录粗削期间的最高读数值
- 检查风动磨削时间和超限长度请记住:实际磨削时间通常只有总周期时间的20-30%。通过减少风动磨削,不需要提高进给率,往往便能缩短加工时间。
磨料和粘结剂的选择
对于缓进给磨削工序,选择陶瓷粘结剂型的氧化铝(Al2O3)砂轮。对于丝锥磨削,选择单晶氧化铝 Al2O3 砂轮。对于使用普通磨料的丝锥槽磨削,选择树脂粘结剂型的砂轮。硬质合金刀具需要金刚石砂轮,最好是混合型粘结剂,如NaxoForce系列或高性能树脂粘结剂。工具钢制铣刀需要混合型、陶瓷型或树脂粘结剂型的CBN。在选择磨料粒度尺寸时,尽可能选择大的磨料粒度尺寸,同时留意角半径要求和表面精整限制。请记住:若把磨料颗粒尺寸减半,相同体积可以纳入八倍多的颗粒,相同接触面积可以纳入四倍多的颗粒。这样可以增大摩擦,减少冷却液的输送。
在进行磨削之前,还要询问操作员所遇到的主要问题。这些问题包括:
- 砂轮现在或以前是否有变形?
- 是否碰到过烧伤或震颤?
- 程序是否稳定?
- 冷却液供应效果如何?是否在整个生产班次中都一样?
- 夹具刚性是否足够?是否发生震动?
- 能否保持尺寸稳定性?
运行
若使用陶瓷粘结型砂轮,在安装砂轮之前,先要对砂轮做音响检查!在金属法兰和使陶瓷砂轮之间使用塑料缓冲垫。使用扭力扳手上紧法兰螺钉。除非给出其它扭矩值,否则对次生孔隙度砂轮使用大约30 Nm的扭矩。具有金属本体的超磨砂轮不需要塑料法兰,也不需要扭力扳手。
若感觉特定砂轮的现有参数合理,则使用新的砂轮规格重复使用这些参数并比较结果。
假设您要运行陶瓷砂轮测试,而且只有几个小时进行测试,不妨将测试砂轮的直径降低到新砂轮和短齿砂轮直径的一半。通常,新砂轮的检查结果非常好,但性能随直径变小而降低。请记住:100毫米直径等于314毫米轮周,因此分担同样工作负荷的磨料颗粒就会少得多。
砂轮修整参数
假设您碰到一个没有历史数据的新磨削任务。若程序允许在配有旋转金刚石滚轮的整形器上对砂轮进行修整,开始先进行同步修整,将速率比qd设为0.8,对于普通磨料而言,将金刚石滚轮进给率ad设为0.5 µm - 1 µm/转。若使用CBN,则将进给率减为0.2 µm/转。NaxosForce粘结剂系列也提供可以修整的金刚石砂轮。
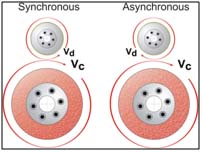
同步和异步修整
整形滚轮具有限定半径,允许使用两根机床轴联动而形成理想的轮廓,从而能够修整砂轮轮廓。在这种情况下,进给率vd 的选择应使得重合度ud为4-6。重合度ud越小,砂轮的研磨度和自由切削程度就越大。横向进给率 vd取决于砂轮速率比 RPM (ns) 和滚轮半径(r)。本文末尾列有横向进给率的公式。
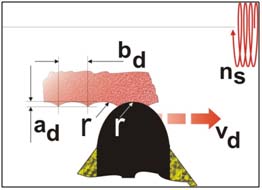
整形滚轮的进给率 vd
磨削参数
若要确定进给率(vw),使用按每毫米砂轮宽度每秒去除材料体积(mm3) (mm3/mm/sec)给出的特定材料率Q’w (Q-prime):Q’w = (进给率vw x 切削深度ae) / 60。作为起点,以下数值可能有所帮助:
- 缓进给磨削硬化钢:5 - 10 mm/mm/s
- 缓进给磨削宇航镍合金: 10 to 20 mm3/mm/s
- 使用树脂粘接砂轮凹槽磨削丝锥: 10 to 20 mm3/mm/s
- 凹槽磨削整体硬合金铣刀: 6 to 12 mm3/mm/s
这些数值取决于机床刚性、工件夹持、磨削材料的硬度和微结构。
如果可能,使用向下磨削模式进行磨削,这样产生的作用力较小,从而能够降低烧伤和工件弯曲变形的风险。根据磨削工艺要求,应将行程数目尽可能保持在较低水平。为了降低加工时间,最好降低行程数目,而非提高进给率。然而,若力求降低加工时间,而且必须在提供切削深度或进给率之间做出选择,那么最好提高进给率,这样可以提高砂轮的研磨度和自由切削程度。
评估
在对任何特定程序做出过多改变之前,先运行一段时间,若使用普通磨料,最好完成一个砂轮的整个使用寿命。
此外还要记住,良好工程设计是一次只改变一个参数,观察改变,做出评估,然后才做进一步调整。
测量部件的尺寸准确性、毛刺形成情况和磨削损伤(烧伤)。鉴于您已经去除了不必要的行程,进一步缩短周期时间可以提高进给率。为了降低砂轮损耗,应减少修整进给。例如,连续修整缓进给可将每转进给率从0.8微米降低到0.6微米/转。最好是迫使砂轮出现故障或烧伤。出于这一目的,特别是烧伤,可能就要产生一些次品。
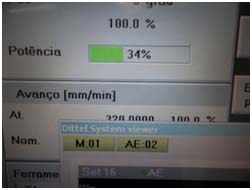
缓进给磨床上的负荷读值
若电流计读值为最大负荷的20%,则可以按20%逐级提高进给率。若电流计读值为60%,则按10%逐级提高。同样,要记住目标在于稳定的程序。我们追求的不是一开始看起来很好,但到下一次换班却会出故障的结果。一旦达到限度,无论是砂轮出现故障还是烧伤,则要按20%降低进给率,以便达到程序稳定性的舒适范围。
您观察到了什么?砂轮表现如何?如果出现变形,则表明存在以下一种或多种情况:
- 砂轮硬度不够
- 表面速度过低(按3-5米/秒逐级提高)
- 进给率过高
- 修整量不够
- 磨料颗粒尺寸太粗
该程序是否造成烧伤?
检查砂轮在修整之后是否锐利。为此要使砂轮完全停下,用指尖触摸感觉。若感觉砂轮光滑,则说明修整参数需要调整;若使用超级磨料,则需要使用修整棒将砂轮打开。检查冷却液的输送情况。喷嘴位置是否正确?冷却液流是否被夹具切断?表面速度可能过高。因此,尝试将砂轮速率比降低3-5 米/秒。您可以提高进给率来提高砂��的自我修锐。为此应按10%逐级进行。
记录
创建自己的试算表,列出研磨部件所需要的每一个行程的所有主要参数。需要记录的参数:
- 砂轮速率比vc
- 切削深度ad
- 进给率vw
- 材料率 Q’w
- 平均芯片厚度hm
- 砂轮研磨度Fa
- 修整率qd和修整量ad
- 电流负荷比例(%)
- 周期时间: tc
发布
与同事分享您的结果,建立一个数据库,以便下一次运行类似测试时能够更快出结果。
使用上述系统方法,我们便能提高程序稳定性和经济价值,确保充分利用现代砂轮的全部潜力。
公式与略语
Fa (研磨度系数 (20-30)) |
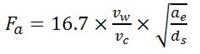 |
Q’w (Q-prime): |
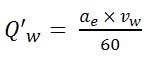 |
hm (平均芯片厚度): |
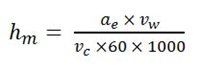 |
vd (整形滚轮的进给率) |
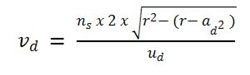 |
qd (修整速率比) |
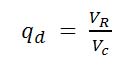 |
qs (磨削速率比) |
 |
- ad = 修整工具每个行程或每转的切削深度(毫米)
- ae = 每个行程的切削深度(毫米)
- ds = 砂轮直径(毫米)
- ns = 砂轮转速(RPM)
- qd = 砂轮和修整滚轮之间的速率比
- tc = 加工时间(秒)
- ud = 整形滚轮的重合度 (4-8)
- vc = 砂轮表面速度(米/秒)
- vd = 整形滚轮的进给率(毫米/分钟)
- VR = 修整滚轮表面速度(米/秒)
- vw = 工件进给率(毫米/分钟)
由Winterthur技术集团首席营销官Walter Graf供稿-2011年
10 十二月 2011