E-Sharp News
Декабрь 2011
Возможности современных шлифовальных кругов часто не используется в полной степени. Причина этого может быть в недостаточно систематическом подходе. Ниже описан один такой систематический метод, который поможет вам определить основные эффективные параметры процесса заточки.
Этот метод применим для заточки с ползучей подачей, а также для заточки канавок фрез и метчиков с использованием традиционных абразивных и суперабразивных материалов.
Рекомендуемый нами подход состоит из 6 этапов. Ряд простых формул используется для определения нескольких ключевых параметров.
Этапы испытания:
- Цель
- Подготовка
- Проведение испытания
- Оценка
- Документирование результатов
- Опубликование результатов
Цель
Во-первых, вы должны четко понимать, что вы (или другие) хотите достичь. Ваши цели могут противоречить друг другу, как например стремление увеличить интенсивность съема материала и в то же время повысить стабильность процесса. Цели могут быть, например, такие:
- Yстранить существующую проблему (прижог, нарушение качества обработки поверхности, нарушение формоустойчивости)
- Yлучшить экономичность процесса – например, повысить долговечность круга
- Yвеличить интенсивность съема материала (т.е. сократить время цикла)
- Испытать новую спецификацию
- Oбеспечить более надежную воспроизводимость результатов
Подготовка
Если вы испытываете существующий процесс, уясните для себя основные параметры и запишите их значения. Эти параметры перечислены ниже.
- Интенсивность съема материала Q’w или Q-prime (помните, что Q’w = (vw x ae)/60 = (скорость подачи vw в мм/мин умножить на глубину резания ae в мм, разделить на 60)
- Скорость круга vc
- Скорость подачи vw
- Общая величина припуска на заточку и глубины резания, и количество проходов
- Проверить, не повреждено ли выпускное отверстие, определить и записать его положение
- Измерить температуру охладителя (утром и вечером) и проверить скорость потока
- Параметры правки круга, такие как отношение скоростей qs, врезная подача, синхронная и асинхронная правка
- Проверить показания амперметра в течение цикла заточки. Записать самое высокое показание во время обдирки
- Проверить потерю времени при подводе круга к заготовке ("шлифование воздуха") и величину перебега круга (выход за деталь). Помните: реальное время заточки часто составляет всего 20 – 30% общего времени цикла, и поэтому сократить время цикла часто бывает проще за счет сокращения “шлифования воздуха”, а не увеличения скорости подачи.
Выбор абразивных материалов и систем связки
При заточке с ползучей подачей, используйте легко крошащийся оксид алюминия (Al2O3) в керамической связке. При заточке резьбы метчика, используйте монокристаллический Al2O3. При заточке канавок метчика традиционными абразивными материалами, используйте керамическое зерно в полимерной связке. Для заточки твердосплавного режущего инструмента необходимы алмазные круги, предпочтительно с гибридной связкой (например, NaxoForce) или c высокоэффективной полимерной связкой. Для обработки фрез из инструментальной стали требуется КБН (кубический нитрид бора) в гибридной, керамической или полимерной связке (в этом порядке предпочтения). При выборе размера шлифовального зерна, старайтесь использовать максимально крупное зерно с учетом требований угловых радиусов и качества обработки поверхности. Помните, что при уменьшении размера зерна в два раза, количество зерен в том же объеме увеличивается в 8 раз, а в зоне контакта – в 4 раза. Это приводит к увеличению трения и мешает распространению охладителя.
Прежде чем запустить какой-либо цикл, узнайте у оператора, с какими он столкнулся основными проблемами. Это такие вопросы, как:
- Теряет (или терял ли) круг свою форму?
- Имели ли место прижог или нестабильная вибрация?
- Стабилен ли процесс?
- Что происходит с подачей охладителя? Одинакова ли она в течение всей смены?
- Сохраняется ли жесткость крепежной оснастки? Происходит ли вибрация?
- Удается ли поддерживать стабильность размеров (формоустойчивость)?
Проведение испытания
Если вы используете круг с керамической связкой, проложите пластмассовые прокладки между металлическим фланцем и кругом перед установкой круга на станок. Затяните винты фланца динамометрическим ключом. Если величина крутящего момента не указана, ориентируйтесь на 20 футо-фунт или примерно 30 Н/м для кругов с вторичной пористостью. Для суперабразивных кругов с металлической основой пластмассовые фланцы и динамометрические ключи не требуются.
Если вам кажется, что существующие параметры для данного круга достаточно эффективны, повторите эти параметры с другой спецификацией круга и сравните результаты.
Предположим, что вы проводите испытание круга на керамической связке, и у вас есть всего несколько часов. Попробуйте уменьшить диаметр испытываемого круга, так чтобы он был примерно на полпути между диаметром нового круга и диаметром полностью сработанного круга. Зачастую новый круг сначала дает прекрасные результаты, но эффективность его работы падает по мере уменьшения диаметра. Помните, что 100мм диаметра соответствуют 314мм длины окружности круга, поэтому при уменьшении диаметра тот же объем работы должен быть выполнен гораздо меньшим количеством абразивных зерен.
Параметры правки
Предположим, что перед вами стоит новая задача по заточке, для которой нет никаких накопленных данных. Если процесс допускает правку кругов на ротационных алмазных валках, начните с синхронной правки, задайте отношение скоростей qd = 0.8, с врезной подачей алмазного валка от 0.5 до 1 микрона за один оборот для традиционных абразивных материалов. При использовании КБН (кубического нитрида бора), врезная подача за один оборот должна быть уменьшена до 0.2 микрона. Существуют также алмазные круги со связками NaxosForce, которые можно править.
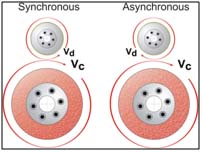
Синхронная и асинхронная правка
При профильной правке круга на валках задается радиус, который позволяет проводить правку, используя две оси станка для получения желаемого профиля. В этом случае скорость подачи vd должна быть выбрана таким образом, чтобы получился коэффициент перекрытия udот 4 до 6. Чем меньше vd тем больше будет режущая способность круга. Скорость горизонтальной подачи (формула которой приведена в конце этой статьи) зависит от частоты вращения круга в об/мин (ns) и радиуса валка (r).
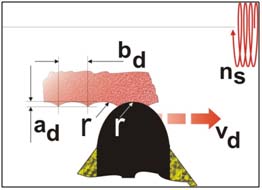
Скорость подачи vd валков для профильной правки
Параметры правки
Чтобы рассчитать скорость подачи vw, используйте определенную величину объема материала Q’w (Q-prime), выраженную как объем снимаемого материала в куб. мм на 1 мм ширины круга в секунду (mm3/mm/сек): Q’w = (скорость подачи vw умножить на глубину резания ae) разделить на 60. Для начала можно использовать следующие величины:
- Заточка с ползучей подачей изделий из закаленной стали: 5 – 10 mm/mm/сек
- Заточка с ползучей подачей изделий из сплавов никеля, применяемых в аэрокосмической промышленности: 10 – 20 mm3/mm/сек
- Заточка канавок метчиков кругами с полимерной связкой: 10 – 20 mm3/mm/сек
- Заточка канавок цельных твердосплавных фрез: 6 – 12 mm3/mm/сек
Эти величины зависят от прочности станка, крепления обрабатываемой детали, твердости и микроструктуры обрабатываемого материала.
По возможности, старайтесь работать в режиме попутного шлифования, поскольку он дает менее интенсивный процесс, что уменьшает риск прижога и деформации обрабатываемой детали. В зависимости от вида заточки, количество проходов нужно стараться свести к минимуму. Чтобы сократить время цикла, лучше уменьшить количество проходов, чем увеличивать скорость подачи. Однако если у вас есть только два варианта для сокращения времени цикла – увеличить глубину резания или увеличить скорость подачи, – то лучше увеличить скорость подачи, т.к. это повышает режущую способность круга.
Оценка
Прежде чем начинать вносить различные изменения в процесс, постарайтесь поработать с ним какое-то время – в идеале, в течение всего периода эксплуатации одного круга, если вы работаете с традиционными абразивными материалами.
Также помните, что правильный подход – это изменить только один параметр за один раз, посмотреть и оценить происходящие изменения, и только потом менять что-то еще.
Проверьте детали на точность размеров, появление заусенцев и нарушение режима заточки (прижог). После исключения ненужных проходов, чтобы еще больше сократить время цикла, увеличьте скорость подачи. Чтобы сократить расход круга, надо уменьшить врезную подачу правки. Например, при непрерывной правке с ползучей подачей, надо уменьшить врезную подачу за один оборот с 0.8 до 0.6 микрон/оборот. В идеале, во время испытания старайтесь довести круг до поломки или до прижога. Для этих целей (в особенности для прижога) вам могут понадобиться бракованные детали.
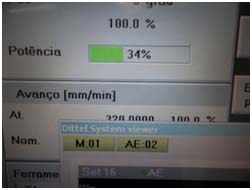
Load reading on a creep-feed grinding machine
Если амперметр показывает 20% максимальной нагрузки, вы можете увеличивать скорость подачи с шагом 20%. Если амперметр показывает 60% максимальной нагрузки, шаг должен быть 10%. Помните, что конечная цель – это стабильный процесс. Нас не интересуют варианты, которые сначала дают замечательный результат, но теряют эффективность к началу следующей смены. Когда вы дошли до предела (разрушение круга или прижог), начинайте постепенно уменьшать скорость подачи с шагом 20%, чтобы найти диапазон стабильности процесса.
Что вы обнаружили? Как вел себя круг? Потеря формоустойчивости круга означает, что имеет место одна или несколько из перечисленных ниже причин:
- Круг слишком мягкий
- Скорость круга слишком низкая (увеличить с шагом 3 – 5 м/сек)
- Скорость подачи слишком высокая
- Недостаточная правка круга
- Абразивное зерно слишком крупное
Произошел ли прижог в процессе обработки?
Проверьте, сохранилась ли острота абразивных зерен после правки круга. Для этого остановите круг и проведите по нему кончиками пальцев. Если поверхность гладкая, вам нужно изменить параметры правки, или же обработать круг бруском для правки (если вы используете суперабразивные материалы). Проверьте также поступление охладителя. В правильном ли положении выпускное отверстие? Не отсекается ли поток охладителя крепежной оснасткой? Возможно, что скорость круга слишком высокая. Попробуйте снизить скорость круга с шагом 3-5 м/сек. Вы также можете увеличить скорость подачи, чтобы увеличить самозатачивание круга. Это можно сделать с шагом 10%.
Документирование результатов
Составьте свою собственную электронную таблицу и введите в нее все основные параметры для каждого прохода, необходимого для заточки детали. Параметры, которые должны быть указаны:
- Cкорость круга vc
- Глубина резания ad
- Cкорость подачи vw
- Интенсивность съема материала Q’w
- Cредняя толщина стружки hm
- Pежущая способность круга Fa
- Oтношение скоростей при правке qd и объем правки ad
- Tоковая нагрузка %
- Время цикла: tc
Опубликование результатов
Старайтесь обменяться результатами с коллегами и создать базу данных, которая ускорит проведение подобных испытаний в будущем.
Используя описанный выше систематический подход, мы можем повысить стабильность и экономичность процесса, и таким образом полностью реализовать потенциал современных шлифовальных кругов.
Формулы и сокращения
Fa (режущая способность круга (20 – 30)) |
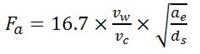 |
Q’w (Q-prime): интенсивность съема материала |
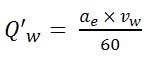 |
hm (средняя толщина стружки): |
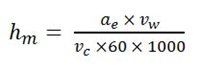 |
vd (скорость подачи валков при профильной правке) |
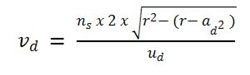 |
qd (отношение скоростей при правке) |
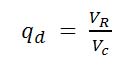 |
qs (отношение скоростей при заточке) |
 |
- ad = глубина резания при правке в мм, за один проход или за один оборот
- ae = глубина резания в мм, за один проход
- ds = диаметр круга в мм
- ns = частота вращения круга в об/мин
- qd = отношение скоростей между кругом и правящим валком
- tc = время цикла в сек
- ud = коэффициент перекрытия валков при профильной правке (4 – 8)
- vc = скорость круга в м/сек
- vd = скорость подачи валков при профильной правке в мм/мин
- VR = скорость валков в м/сек
- vw = скорость подачи обрабатываемой детали в мм/мин
Статья подготовлена Вальтером Графом, руководителем службы маркетинга компании Winterthur Technology Group, 2011г.
10 декабря 2011