Sharp-E 뉴스 레터
2011 년 12 월
사용하고 있는 연삭 휠의 장점을 최대로 활용하기는 쉬운 일이 아닙니다. 다음은 어떻게 연삭공정의 중요한 변수들을 찾는 과정을 설명해 줍니다.
이 방법은 이송속도가 아주느린 일반 크립피드 연삭에 적용할 수 있을 뿐만 아니라 밀링커터나 탭의 플루팅 연삭에도 적용이 가능 합니다.
아래에 추천하는 연삭 테스트 구성 방법은 6가지 단계로 이루어져 있습니다. 중요 변수들을 지정하기 위한 몇가지 간단한 공식도 사용 하였습니다.
공정 순서
1. 목적
2. 준비
3. 테스트
4. 평가
5. 기록
6. 정보 공유
목적
먼저 찾고자 하는 목표가 분명해야 합니다. 몇가지 목표들은 서로 상반되는 경우가 종종 생길 수도 있습니다. 예를 들면 최대의 단위시간당 연삭량과 공정안정 향상을 동시에 달성하기를 원하는 경우. 몇가지 목적의 예를 들면 :
1. 버닝, 표면 조도, 치수 안정등 현재 공정의 문제 해결을 원할때
2. 휠 수명 증가와 같이 생산 공정 안정을 원할때
3. 사이클타임 단축 같은 단위시간당 연삭량을 증가시키고자 할때
4. 새로운 기준으로 테스트 해야 할때
5. 같은 결과를 계속 내고자 할때
준비
현재의 공정에 적용하려면 아래사항들을 정확히 파악하고 기록 하십시요.
1. 단위 시간당 연삭량Q’w 또는 Q-prime ( Q’w = (vw x Ae)/60 = {(이송속도 vw mm/min x 연삭 깊이 ae mm) 를 60으로 나눈 값}
2. 휠 원주속도 Vs
3. 이송 속도Vw
4. 총 연삭 여유, 연삭 깊이Ae와 연삭 횟수
5. 절삭유 노즐의 바른 위치와 상태 점검및 기록
6. 절삭유 온도 측정(아침/저녁)과 유량 점검
7. 드레싱 변수들 예) 휠/드레서 속도비Qs, 드레싱 깊이, 동시 드레싱/개별 드레싱
8. 연삭 공정 중 연삭부하 Load 미터 점검. 황삭시 최대 Load 수치 기록
9. 연삭 없는 공회전 시간 단축 –연삭전 이송및 연삭후 추가이동거리. 실제 연삭시간은 총 사이클타임의 20-30%밖에 되지않는 경우가 종종 있습니다. 무리하게 이송 속도를 증가시키는 것 보다 이런 필요없는 공회전 시간을 줄이는 것이 더 낫습니다.
연삭 입자와 본드 선택
이송속도가 아주느린 크립피드 연삭의 경우 비트리 본드의 알미늄 옥사이드(Al2O3) 휠을 선택하십시요.
탭의 나사산 연삭에는 모노 크리스탈 알미늄 옥사이드 휠을 사용하세요.
탭의 플루팅 연삭에 일반 연삭 휠을 적용하려면 세라믹 입자의 레진 본드를 선택하는 것을 추천 합니다.
초경 절삭 공구의 연삭에는 NaxoForce같은 하이브리드 본드나 고성능 레진본드를 추천 합니다.
공구강이나 고속도강으로된 엔드밀이나 밀링 커터 연삭에는 CBN입자에 하이브리드, 레진이나 비트리 본드 계열을 사용하십시요.
연삭 입자크기를 선정 할때는 가능한 큰치수를 선택하십시요(코너반경이나 표면조도를 고려 하셔야 합니다). 입자크기를 반으로 줄이면 같은 볼륨에 8배나 많은 입자를 넣을 수 있고 연삭시 동일한 접축면적에 4배나 많은 입자를 쓰게 할 수 있습니다. 하지만 이런 경우에는 입자크기가 작아짐으로 인해 마찰 증가와 연삭점으로의 절삭유 유입이 어려워지는 단점이 있습니다.
시작 전에 작업자에게 다음의 질문들을 먼저 해 보시기 바랍니다.
1. 연삭휠의 형상 변화가 있는지?
2. 버닝이나 떨림 현상이 발생하는지?
3. 공정이 안정적인지?
4. 절삭유가 제대로 균일하게 공급되고 있는지?
5. 지그나 고정구가 단단하게 고정되어 있는지? 작업중 떨림이 발생하는지?
6. 연삭된 치수가 안정적으로 유지되는지?
테스트 실시
비트리 계열의 본드 휠을 사용하기전 반드시 플라스틱 망치로 살짝 두드려보아 맑은 소리가 나는지 확인 하십시요. 기공이 있는 일반 휠들의 체결 시에는 특별한 토오크 규정이 없는 경우 토오크 렌치를 사용하여 20 foot*pounds나30 Nm로 조이십시요. 금솟몸체로 된 CBN/다이아몬드 휠의 체결은 따로 토오크렌치를 사용할 필요가 없습니다.
현재 사용중인 연삭조건에 만족하시는 경우 새로운 휠에도 그대로 적용해 보시고 결과를 비교하십시요.
만약 비트리휠을 테스트할 시간이 그리 충분치 않으시다면 시험할 휠의 외경을 사용가능 범위의 반으로 잘라서 테스트 하십시요. 종종 새 휠이 외경이 줄어감에따라 성능저하가 발생하기도 한답니다. 작아보이는100mm 외경도 원주길이는 314mm나 되기때문에 같은 연삭부하를 상대적으로 적은 입자수로 버텨내야 한다는 것을 의미 합니다.
드레싱 변수들
이전경험 이나 데이터없이 새로운 연삭작업을 해야하는 상황의 경우에는 기계내에서 로터리 다이아몬드 드레서로 드레싱이 가능하다면 같은 방향 회전드레싱을 속도비 (Qd) 0.8로 실시해 보십시요.
- 일반 연삭휠: 1회전당 0.5-1um 드레싱 깊이(Ad)로
- CBN휠 : 줄여서 1회전당 0.2um 드레싱 깊이(Ad)로
NaxoForce 본드계열에서는 드레싱이 가능한 다이아몬드 휠을 찾을 수 있습니다
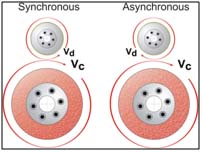
같은 방향 회전드레싱과 반대 방향 회전드레싱
형상드레싱 롤은 지정된 반경을 가지고 원하는 형상대로 기계의 축들을 움직여 드레싱 작업을 합니다. 이경우 이송속도 Vd 선택시 오버랩 비율(Ud) 이 4-6정도가 되도록 합니다. 오버랩 비율이 적을 수록 휠은 거칠게 드레싱 됩니다. 횡방향 이송속도Vd는 휠 RPM Ns 과 롤 드레서 반경r에 따라 다릅니다. 자세한 내용은 기사 뒤편을 참조하세요.
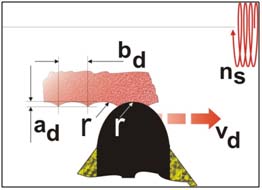
형상드레싱 롤의 횡방향 이송속도 Vd
연삭 변수들
이송속도Vw를 찾기위해서는
초당 휠폭1mm당 연삭량 Q’w (Q프라임이라고 부름) 단위를 사용합니다.
시작시 사용할 수치들은
- 열처리강 크립피드 연삭의 경우 : 5-10mm3/mm/sec
- 항공기용니켈합금강 크립피드 연삭의 경우 : 10-20mm3/mm/sec
- 레진본드휠로 공구강 탭 플루팅 연삭 : 10-20mm3/mm/sec
- 초경 엔드밀의 플루팅 연삭 : 6-12 mm3/mm/sec
위의 수치들은 기계및 장비의 견고함, 공작물 치구상태, 연삭재질의 경도및 조직 상태에 따라 다릅니다. 가능하다면 하향 연삭 방식을 사용하는 것이 연삭력을 적게 발생시켜 재질의 휨이나 버닝 발생을 줄일 수 있습니다. 연삭조건에 따라 다르겠지만 연삭pass수는 가능한 한 최소로 유지하십시요. 사이클 타임을 줄이려면 이송속도의 증가보다는 연삭pass수를 줄이십시요.
만약 사이클 타임 단축이 목적이라서 연삭깊이나 이송속도 변경중 하나를 선택하셔야 한다면 이송속도 증가를 택하시는 것이 좋습니다. 결과적으로 휠이 좀더 거칠게 공작물에 밀어붙이는 결과를 가져옵니다.
평가
많은 변경을 공정에 바로 적용하기전에 조금 더 테스트를 해 보세요 (일반 휠인 경우 휠 하나를 다 쓸때까지).
좋은 엔지니어링 습관 중의 하나는 한번에 변수하나씩을 바꾸어 테스트하고, 변화를 관찰, 테스트 결과를 평가한 후에 다음 변경으로 진행하는 것 임을 명심하시기 바랍니다.
가공된 부품의 치수정밀도, 버어발생과 버닝현상등을 확인하십시요. 불 필요한 pass를 모두제거한 후에는 이송속도를 높이십시요. 휠 수명을 높이려면 드레싱 깊이를 줄이십시요. 예를 들어 연속드레싱의 크립피드 연삭의 경우 회전당 그레싱 깊이를 0.8um에서 0.6um 로 줄여 보십시요. 휠이 부스러지거나 버닝이 나는 한도까지 테스트를 해 보십시요.
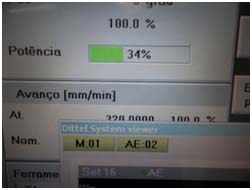
크립피드 연삭 전용기의 LOAD미터계에 관하여
연삭부하를 표시하는 암페어 미터가 최고부하의 20%정도인 경우 20%씩 단계적으로 이송속도를 높여 보세요. 60%에 도달하면 10%씩 높여가며 테스트 하십시요.
이때에 기억하셔야 할것은 “안정된 연삭공정의 유지”가 관건 입니다. 새롭게 설정된 조건으로 처음과 나중이 균일한 결과를 낼 수 있어야 합니다.
원하는 목표와 한계에 도달했다고 생각되는 지점 (휠 마모가 심해지거나 버닝이 생기는 지점)에서 이송속도를 20%줄여 안정적으로 공정이 계속 유지될 수 있도록 해 주십시요.
어떤 결과를 관찰하셨나요?
휠은 어떻게 반응하나요?
휠 형상이 변경된 경우 아래의 가능한 원인들을 재 점검하세요.
- 휠이 너무 푸석푸석함(soft)
- 휠 원주속도가 낮음 ( 3-5 m/s씩 단계적으로 증가시킴)
- 이송속도가 빠름
- 드레싱량이 부적당함
- 휠 입자크기가 너무 큼
공정 중 버닝 현상이 나타나나요?
드레싱후 휠이 날카로운지 확인하세요. 드레싱 후 손톱으로 드레싱된 면을 긁어보아 부드럽게 느껴지면 드레싱 변수를 변경해야 할 필요가 있습니다 (CBN이나 다이아몬드 휠의 경우 화이트 스틱을 사용합니다).
그다음 절삭유 상태를 확인하세요.
휠의 원주 속도가 너무 높은가요? ( 3-5 m/s씩 단계적으로 감소시킴)
기록
테스트 후에는 결과를 챠트나 도표로 만드신 후, 각 부품별로 연삭에 필요한 변수 리스트로 만들어 사용하면서 계속 업데이트 하십시요.
1. 휠 원주속도 Vc
2. 연삭깊이 Ad
3. 이송속도 Vw
4. 단위 시간당 연삭량 Q’w
5. 평균 연삭 칩 두께 Hm
6. 연삭 거칠기 계수 Fa
7. 드레싱 비율 Qd과 드레싱 량 Aa
8. 연삭 부하 Load값 %
9. 사이클 타임 Tc
정보 공유
테스트를 통해 얻어진 결과들을 데이터베이스로 만들어 동료들과 같이 사용하면서 계속 업데이트 하십시요. 이 기사에서 추천하는 방법을 기본으로 계속 테스트를 진행하다보면 휠의 성능을 극대화 시키면서 연삭 공정의 안정과 경제적 절감을 이룰 수 있을 것입니다.
공식및 사용기호
Fa = 연삭 거칠기 계수 (20-30사이) |
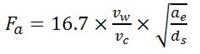 |
Q’w = 단위 시간당 연삭량 (Q-prime) |
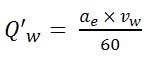 |
Hm = 평균 연삭 칩 두께 |
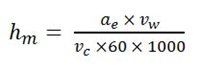 |
Vd = 형상드레싱 롤의 이송속도 |
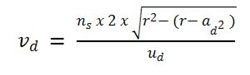 |
Qd = 드레싱 비율 |
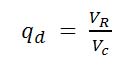 |
Qs = 속도비율 |
 |
· Ad = 드레서의 pass당 또는 회전당 절삭깊이
· Ae = pass 절삭깊이 (mm)
· Ds = 연삭 휠 외경 (mm)
· Ns = 연삭 휠 (RPM)
· Qd = 연삭휠과 드레서롤의 속도비
· Tc = 사이클 타임 (sec)
· Ud = 형상 드레싱 롤의 오버랩 비율 (4-8)
· Vc = 휠 원주속도 (m/s)
· Vd =형상 드레싱 롤의 이송속도 (mm/min)
· Vr =드레싱 롤의 원주속도(m/s)
· Vw = 공작물 이송속도(mm/min)
이 기사는 Winterthur 그룹 CMO 인 Walter Graf씨가 제공하였습니다. Winterthur Technology Group 2011
10 12월 2011