Biuletyn Sharp E
Grudzień 2011
Często pełny potencjał ściernic nie jest całkowicie wykorzystany. Może to być spowodowane brakiem systematycznego podejścia. Poniższy opis przedstawia jedno z takich systematycznych podejść, które mogą pomóc w ustaleniu skutecznych kluczowych parametrów procesów szlifowania.
Metodologia ta może być zastosowana do konwencjonalnego szlifowania z pełzającym posuwem, jak również do szlifowania rowków frezów i gwintowników z użyciem materiałów konwencjonalnych lub super-ściernych.
Zalecane podejście sprowadza się do sześciu etapów procesu. Kilka prostych formuł służy do określenia niektórych kluczowych parametrów.
Etapy procesu:
- Cel
- Przygotowanie
- Praca
- Ocenianie
- Zapisywanie
- Opublikowanie
Cel
Po pierwsze, miej jasność, co ty, lub inni, chcecie osiągnąć. Niektóre cele mogą być sprzeczne ze sobą, jak np. dążenie do wyższych szybkości usuwania, przy równoczesnym staraniu się osiągnięcia lepszej stabilności procesu. Celem mogą na przykład być:
- Rozwiązanie istniejącego problemu (spalanie, wykańczanie powierzchni, stabilność wymiarowa)
- Większa oszczędność procesu, jak np. dłuższa trwałość kół
- Wysoka szybkość usuwania materiału, czyli krótszy czas cyklu
- Nowa specyfikacja do zbadania
- Bardziej powtarzalne wyniki
Przygotowanie
Jeśli zadaniem jest istniejący proces, należy zapoznać się z kluczowymi zagadnieniami i ich zapisem. Należą do nich:
- Szybkość usuwania materiału Q’w lub Q-prime (pamiętaj Q’w = (vw x ae)/60 = (vw itempo posuwu w mm/min x głębokość cięcia ae w mm podzielona przez 60)
- Szybkości koła vc
- Tempo posuwu vw
- Łączna suma luzu szlifowania i głębokości cięcia ae oraz liczba cięć
- Sprawdzanie, czy dysze nie sa uszkodzone, ustalanie i odnotowywanie pozycji dyszy
- Mierzenie temperatury płynu chłodzącego (rano i wieczorem) i sprawdzić natężenia przepływu
- Parametry obciągania, takie, jak stosunek posuwu qs, synchroniczne i asynchroniczne obciąganie
- Sprawdzanie licznika Amp podczas cyklu szlifowania. Zapisywanie najwyższego odczytu podczas obróbki zgrubnej
- Sprawdzanie czasu szlifowania i długości przekroczenia. Pamiętaj: rzeczywisty czas szlifiwania wynosi często tylko 20 do 30% całkowitego czasu cyklu. Zyski w redukcji czasu cyklu można często osiągnąć przez zmniejszenie qs, zamiast zwiększenia tempa podawania.
Wybór materiałów ściernych I systemów spajania
Na szlifowanie z pełzającym posuwem, wybierz kruchy tlenek glinu (Al2O3) w spoiwie ceramicznym. Dla szlifowania gwintownika wybierz monokrystaliczny Al2O3. Dla szlifowania rowków gwintowników z użyciem konwencjonalnych materiałów ściernych, wybierz ceramiczne ziarno w spoiwie żywicy. Węglikowe narzędzia tnące wymagają ściernic diamentowych, najlepiej w hybrydowych spoiwach, takich jak serie NaxoForce, albo spoiwa żywicy o wysokiej wydajności. Frezy ze stali narzędziowej wymagają CBN, albo w spoiwach hybrydowych, ceramicznych lub żywicy, w tej kolejności wyboru. Przy wyborze wielkości ziarna, wybierz możliwie jak największy rozmiar ziarna, mając na uwadze wymagania promieni wierzchołka noża tokarskiego i ograniczenia powierzchni wykończeniowej. Pamiętaj, że zmniejszenie o połowę wielkości ziarna dopuszcza osiem razy więcej ziarna w tym samym woluminie, lub cztery razy więcej ziarna na tej samej powierzchni kontaktu. Zwiększa to tarcie oraz redukuje transport płynu chłodzącego.
Przed uruchomieniem jakichkolwiek cykli, zapytaj również operatora o główne problemy, jakie wystąpiły w przeszłości. Do pytań tych należą:
- Czy koło traci lub traciło formę?
- Czy doświadczono spalania lub trzęsienia?
- Czy process jest stabilny?
- Jak zachowuje się doprowadzanie chłodziwa? Czy jest ono takie samo przez okres całej zmiany?
- Czy zamocowanie jest sztywne? Czy występują wibracje?
- Czy daje się utrzymać stabilność wymiarową?
Praca
Jeśli korzystasz ze ściernicy z ceramicznego spoiwa, przed zamontowaniem ściernicy, opierścieniuj ją! Korzystaj z suszki ze sztucznego tworzywa między metalowym kołnierzem i ceramiczną ściernicą. Dokręć śruby kołnierza dynamometrycznym kluczem. O ile nie zostały podane jekiekolwiek wartości momentu obrotowego, należy stosować 20 ściernic 20 foot-pounds lub około 30 Nm dla wywołanej porowatości ściernicy. Super-ścierne koła z metalowym korpusem nie wymagają plastikowych kołnierzy, ani kluczy dynamometrycznych.
Jeśli uważasz, że istniejące parametry dla danej ściernicy są uzasadnione, powtórz te parametry dla nowej specyfikacji ściernicy i porównaj wyniki.
Załóżmy, że prowadzisz test ściernicy ceramicznej i masz tylko kilka godzin na przeprpwadzenie tego testu. Rozważ zmniejszenie średnicy testowanej ściernicy w połowie drogi pomiędzy nową ściernicą i końcówką. Często nowa średnica daje doskonałe wyniki, podczas gdy wydajność maleje w miarę, jak średnica staje się mniejsza. Pamiętaj, że średnica 100 mm równa się 314 mm w obwodzie ściernicy, a więc znacznie mniej ściernych ziaren musi dzielić to samo obciążenie pracą.
Parametry obciągania
Załóżmy, że masz do czynienia z nowym zadaniem szlifowania, dla którego nie ma danych historycznych. Jeśli proces pozwala na obciągnięcie ściernicy na maszynie z obrotowymi diamentowymi rolkami, zacznij od synchronicznego obciągania, ustawiając stosunek prędkości qd na 0,8, z diamentową rolką posuwu wgłębnego ad 0,5 µm do 1 µm na obrót dla konwencjonalnych materiałów ściernych. W przypadku korzystania z CBN, zmniejszyć posuw wgłębny na obrót do 0,2 µm. Rodzina spoiw NaxosForce oferuje również ściernice diamentowe pozwalające na obciąganie.
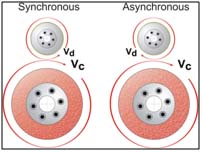
Synchroniczne i asynchroniczne obciąganie
Utwórz funkcję obciągania ściernic o określonym promieniu, który pozwala na obciaganie profili do szlifowania za pomocą dwóch osi maszyny do generowania odpowiedniego profilu. W tym przypadku tempo posuwu vd powinno być dobrane tak, żeby powstał stosunek zachodzenia na siebie ud od 4 do 6. Im mniejsze zachodzenie na siebie ud, tym bardziej agresywnie i automatowo będzie się ściernica zachowywać. Boczne tempo posuwu vd, formuła, którą znajdziesz na końcu tego artykułu, zależy od obrotów koła (ns) i promienia rolki (r).
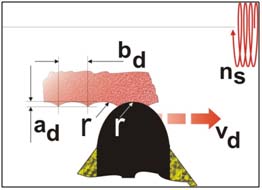
Tempo posuwu vd rolki obciągania
Parametry szlifowania
Aby ustalić tempo posuwu vw, skorzystaj z określonego stosunku materiałów Q’w (Q-prime), podanego w objętości materiału usuniętego (mm3) na mm szerokości ściernicy na sekundę (mm3/mm /sek): Q’w = (tempo posuwu vw x głębokość cięcia ae) / 60. Następujące wartości mogą pomóc, jako punkt wyjściowy
- Stal hartowana do szlifowania posuwem pełzającym: 5 do 10 m m3/mm/sek
- Stopy niklu przestrzeni powietrznej do szlifowania posuwem pełzającym: 10 do 20 mm3/mm/sek
- Szlifowanie rowków gwintowników ściernicami ze spoiwa żywicznego: 10 do 20 mm3/mm/sek
- Lite frezy węglikowe do szlifowania rowków: 6 do 12 mm3/mm/sek
Wartości te zależą od sztywności obrabiarki, mocowania przedmiotu obrabianego, twardości oraz mikrostruktury szlifowanego materiału.
Jeśli to możliwe, pracuj w trybie szlifowania do dołu, ponieważ wytwarza to mniejsze siły, które z kolei zmniejszają ryzyko spalania i zginania przedmiotu. W zależności od zadania szlifowania, liczba przejść powinna możliwe jak najniższa. Aby skrócić czas cyklu, lepiej jest zmniejszyć liczbę przejść, niż zwiększyć tempo posuwów. Jednakże, jeśli celem jest skrócenie czasu cyklu i trzeba wybierać pomiędzy wzrostem głębokości cięcia lub tempa posuwu, to lepiej jest zwiększyć tempo posuwu, ponieważ sprawia to, że ściernica jest bardziej agresywna i automatowa.
Ocenianie
Przed dokonaniem zbyt wielu zmian w danym procesie, popracuj najpierw przez pewien czas, najlepiej przez pełny okres żywotności jednej ściernicy, jeśli używasz konwencjonalnych materiałów ściernych.
Należy również pamiętać, że dobrą techniką jest zmiana tylko jednego parametru na raz, obserwowanie zmian, ocenienie i dopiero wtedy dokonanie dalszych regulacji.
Mierz komponenty w celu zapewnienia wymiarowej dokładności oraz uniknięcia tworzenia zadziorów i niewłaściwego szlifowania (spalania). Zakładając, że wyeliminowałeś niepotrzebne przejścia, w celu dalszego skrócenia czasu cyklu zwiększ tempo posuwu. Aby zmniejszyć zużycie ściernicy, zmniejsz posuw wgłębny. Na przykład, w ciągłym obciąganiu, posuw pełzający zmniejsza posuw wgłębny na obrót od 0,8 mikrona do 0,6 mikrona / obr. Najlepiej jest zmusić ściernicę do awarii lub spalenia. W tym celu, a w szczególności spalania, możesz potrzebować jakichś wybrakowanych komponentów.
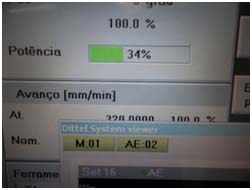
Załaduj odczyt na szlifierce o pełzającym posuwie
Jeżeli licznik Amp pokazuje 20% maksymalnego obciążenia, można zwiększyć stopniowo tempo posuwu w 20% skokach. Jeżeli odczyt Amp jest na poziomie 60%, przyjmij 10% skoki. I pamiętaj, że celem jest stabilność procesu. Nie dążymy do wyników, które świetnie wyglądają na początku ale spadną przy następnych zmianach. Po osiągnięciu limitu, czyli doprowadzeniu do awarii lub spalania ściernicy, cofnij tempo posuwu o 20% do osiągnięcia strefy komfortu stabilności procesu.
Co zaobserwowałeś? Jak się zachowywała ściernica? Utrata formy oznacza jedną lub kilka z następujących rzeczy:
- Ściernica jest zbyt miękka
- Prędkość obwodowa jest zbyt niska (zwiększ stopniowo od 3 do 5 m/sek)
- Tempo posuwu jest zbyt wysokie
- Ilość obciagnięć jest niewystarczająca
- Wielkość ziarna jest nadmierna
Czy proces doprowadził do spalenia?
Sprawdź, czy koło jest ostre po obciągnięciu. Aby to zrobić, zatrzymaj całkowicie ściernicę i zbadaj ją czubkami palców. Jeżeli ściernica wydaje się się gładka, twoje parametry obciągania wymagają korekty, bądź też ściernica musi zostać otwarta drążkiem obciągania w przypadku korzystania z super-ściernych materiałów. Sprawdź dostawę płynu chłodzącego. Czy dysza jest we właściwej pozycji? Czy przepływ chłodziwa jest przez coś odcięty? Prędkość skrawania może być zbyt wysoka. Dlatego spróbuj zmniejszyć prędkość koła od 3 do 5 m/sek. Możesz zwiększyć tempo posuwu w celu zwiększenia samoostrzenia się ściernicy. W tym celu należy użyć skoki 10%.
Zapisywanie
Stwórz swój własny arkusz kalkulacyjny obejmujący wykaz wszystkich podstawowych parametrów dla każdego z przejść, które są potrzebne do szlifowania elementów. Parametry, które muszą być zapisane, to:
- Prędkość ściernicy vc
- Głębokość cięcia ad
- Tempo posuwu vw
- Stosunek materiałów Q’w
- Średnia grubość wióra hm
- Agresywności ściernicy Fa
- Stosunek obciągania qd i ilość obciągnięć ad
- Obciążenie Amp w %
- Czas cyklu: tc
Opublikowanie
Podziel się swoimi wynikami z kolegami i buduj bazę danych, która da ci szybsze wyniki następnym razem, kiedy będziesz przeprowadzać podobny test.
Za pomocą systematycznego podejścia, jak opisano, możemy zwiększyć stabilność procesu i ekonomikę, oraz zapewnić wykorzystanie w pełni potencjału nowoczesnych ściernic.
Formuły i skróty
Fa (czynnik agresywności (20 do 30)) |
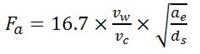 |
Q’w (Q-prime): |
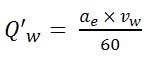 |
hm (przeciętna grubość wióra): |
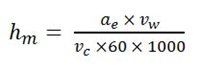 |
vd (tempo posuwu formowych rolek obciągania) |
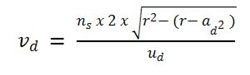 |
qd (stosunek prędkości obciągania) |
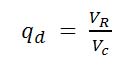 |
qs (stosunek prędkości szlifowania) |
 |
- ad = głębokość cięcia narzędzi obciągania na przejście lub obrót w mm
- ae = głębokość cięcia na przejście w mm
- ds = średnica ściernicy w mm
- ns = RPM ściernicy
- qd = stosunek prędkości pomiędzy ściernicą i rolką obciągajacą
- tc = czas trwania cyklu w sekundach
- ud = współczynnik zachodzenia na siebie formowych rolek obciągajacych (4 do 8)
- vc = prędkość powierzchni ściernicy w m/sek
- vd = tempo posuwu formowych rolek obciągajacych w mm/min
- VR = prędkości powierzchni rolki obciągajacej w m/sek
- vw = tempo posuwu elementu obrabianego w mm/min
Artykuł dostarczony przez Waltera Grafa, Dyrektora ds. Marketingu w Winterthur Technology Group 2011
10 grudnia 2011