Der Sharp-E Newsletter
Dezember 2011
Das volle Potential von Schleifscheiben wird oftmals nicht voll ausgenutzt, möglicherweise weil der Anzatz hierzu nicht systematisch ist. Im folgenden wird ein systematische Ansatz beschrieben, mit dem effektive Schlüsselparameter des Schleifprozesses etabliert werden können.
Die Methode kann fürs herkömmliche Tiefschleifen sowie das Nutenschleifen auf Fräsern und Gewindebohrern gleichermaßen angewendet werden, mit konventionellen oder superabrasiven Schleifmitteln.
Die Methode ist in sechs Schritte untergliedert. Einige der Schlüsselparameter werden mittels einfacher Formeln definiert.
Prozessschritte:
1. Zielsetzung
2. Vorbereitung
3. Durchführung
4. Auswertung
5. Aufzeichnung
6. Veröffentlichung
Zielsetzung
Seien Sie sich darüber klar, was Sie erreichen wollen. Bei den Zielen kann es manchmal zu Konflikten kommen, zum Beispiel wenn höhere Abtragsraten bei gleichzeitig besserer Prozessstabilität erreicht werden sollen. Einige Ziele sind:
1. Beheben eines bestehenden Problems (Brandmarken, Oberflächenqualität, gleichbleibende Maße)
2. Verbesserung des Prozesses, z.B. durch längere Scheibennutzdauer
3. Höhere Abtragsraten, d.h. kürzere Zykluszeiten
4. Testen neuer Vorgaben
5. Wiederholbare Ergebnisse
Vorbereitung
Wenn es sich bei der Aufgabe um einen bereits bestehenden Prozess handelt, machen Sie sich mit den Hauptpunkten vertraut und zeichnen Sie diese auf:
1. Materialabtragsrate Q’w oder Q-prime (wobei Q’w = (vw x ae)/60 = (Vorschub vw in mm/min x Schnitttiefe ae in mm, geteilt durch 60)
2. Scheibengeschwindigkeit vc
3. Vorschub vw
4. Gesamtbetrag der Schleifzugabe und Schnitttiefe ae und Anzahl Schnitte
5. Düsen auf Schäden prüfen, Düsenposition festlegen und aufzeichnen
6. Kühlmitteltemperatur messen (morgens und abends) und Durchflussmenge prüfen
7. Abrichtparameter wie Geschwindigkeitsverhältnis qs, Zustellung, synchrones oder asynchrones Abrichten
8. Amp-Messer während des Schleifzyklus prüfen. Die höchsten Werte beim Schruppschleifen aufzeichnen
9. Luftschleifzeit und Nachlaufdauer prüfen. Die tatsächliche Schleifdauer ist oftmals nur 20 bis 30% der Gesamtzyklusdauer. Die Zyklusdauer kann oftmals durch Reduzieren des Luftschleifens erreicht werden, ohne Erhöhung der Vorschübe.
Wahl der Schleifmittel und Bindungssysteme
Fürs Tiefschleifen wird Edelkorund (Al2O3) in Keramikbindung gewählt. Fürs Gewindebohrerschleifen wählen Sie monokristallines Al2O3. Fürs Nutenschleifen von Gewindebohrern mit konventionellen Schleifmitteln wird ein keramisches Schleifkorn mit Harzbindung gewählt. Für Hartmetallwerkzeuge sind Diamantscheiben erforderlich, vorzugsweise mit Hybridbindung, wie NaxoForce, oder Hochleistungsharzbindung. Fräser aus Werkzeugstahl erfordern CBN mit entweder Hybrid-, Keramik- oder Harzbindung (in dieser bevorzugten Reihenfolge). Wählen Sie dabei die größtmögliche Korngröße, unter Berücksichtigung der Eckenfasen und Oberflächenqualität. Beachten Sie, dass bei Halbieren der Korngröße die achtfache Kornanzahl im selben Volumen enthalten ist. Dies erhöht die Reibung und reduziert die Kühlmittelzuführung.
Wenn Sie eine Scheibe mit Keramikbindung verwenden und es stehen Ihnen fürs Testen nur wenige Stunden zur Verfügung, reduzieren Sie den Durchmesser der Testscheibe auf halbwegs zwischen neuer Scheibe und Scheibenstummel. Mit einer neuen Scheibe werden oft ausgezeichnete Ergebnisse erzielt; die Leistung lässt dann mit kleiner werdendem Durchmesser nach. 100 mm Scheibendurchmesser entspricht 314 mm Umfang, bei kleinerem Durchmesser wird jedes einzelne Schleifkorn stärker belastet.
Abrichtparameter
Wenn Sie sich einer neuen Schleifaufgabe gegenübersehen, für die noch keine Daten vorliegen, beginnen Sie mit dem synchronen Abrichten der Scheibe mit Diamantabrichtrollen, wenn dies im Prozess möglich ist. Setzen Sie das Geschwindigkeitsverhältnis qd auf 0.8, mit Diamantrollenzustellung ad von 0.5 µm bis 1 µm pro Drehung für herkömmliche Schleifmittel. Abrichtbare Diamantscheiben sind auch mit NaxosForce-Bindung erhältlich.
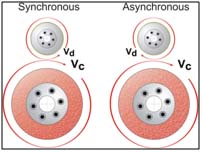
Synchrones und asynchrones Abrichten
Formabrichtrollen haben einen definierten Radius, mit dem Profile auf Scheiben übertragen werden, indem mit zwei der Maschinenachsen das Profil erzeugt wird. In diesem Fall sollte der Vorschub vd so gewählt werden, dass ein Überlappverhältnis ud von 4 bis 6 resultiert. Je kleiner die Überlappdistanz ud, desto aggressiver verhält sich die Scheibe. Der laterale Vorschub vd, dessen Formel sich am Ende dieses Artikels befindet, richtet sich nach der Scheibendrehzahl U/min (ns) und dem Radius der Rolle (r).
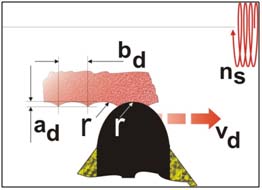
Vorschub vd einer Formabrichtrolle
Schleifparameter
Um den Vorschub vw zu ermitteln, wird der spezifische Materialabtrag Q’w (Q-prime) in abgetragenem Materialvolumen (mm3) pro mm Scheibenbreite pro Sekunde (mm3/mm/sec) angegeben: Q’w = (Vorschub vw x Schnitttiefe ae) / 60. Die folgenden sind gute Anfangswerte:
• Tiefschleifen gehärteter Stahl: 5 bis10 mm/mm/s
• Tiefschleifen Luftfahrt-Nickellegierungen: 10 bis 20 mm3/mm/s
• Nutenschleifen von Gewindebohrern mit harzgebundenen Scheiben: 10 bis 20 mm3/mm/s
• Nutenschleifen auf Hartmetallfräsern: 6 bis 12 mm3/mm/s
Diese Werte richten sich nach der Steifheit der Werkzeugmaschine, der Werkstückhalterung, der Härte und der Mikrostruktur des zu schleifenden Materials.
Wenn möglich, schleifen Sie in “Down-grinding” Modus , da dies geringere Lasten erzeugt, die wiederum das Risiko von Brandmarken und Durchbiegen des Werkstücks reduzieren. Je nach Schleifaufgabe sollte die Anzahl von Durchgängen so niedrig wie möglich gehalten werden. Es ist besser, zum Reduzieren die Anzahl der Durchgänge zu reduzieren als den Vorschub zu erhöhen. Wenn Zykluszeit reduziert werden soll und zwischen Erhöhen der Schnitttiefe oder schnellerem Vorschub gewählt werden muss, ist ein schnellerer Vorschub die bessere Option, da die Scheibe dann aggressiver schleift
Auswerten
Bevor Sie einen Prozess abändern, führen Sie ihn für eine Weile durch, idealerweise für die gesamte Nutzdauer einer Scheibe, wenn Sie mit herkömmlichen Schleifmitteln arbeiten.
Beachten Sie außerdem, dass das Ändern nur jeweils eines Parameters gute Praxis ist, beobachten Sie gemachte Änderungen, werten Sie diese aus und nehmen Sie erst dann weitere Änderungen vor.
Messen Sie alle Teile und prüfen Sie die Genauigkeit der Werte, auf eventuelle Gratformung auf dem geschliffenen Teil und Schleiffehler (Brandmarken). Davon ausgehend, dass Sie unnötige Durchgänge eliminiert haben, können Sie den Vorschub erhöhen, um die Zykluszeit weiter zu reduzieren. Um den Scheibenverschleiß zu reduzieren, verwenden Sie kleinere Abrichtzustellungen. Beim kontinuierlichen Tiefschleifen reduzieren Sie die Zustellung pro Umdrehung von 0.8 Mikrometer auf 0.6 Mikrometer. Idealerweise arbeiten Sie mit der Scheibe an ihrer Leistungsgrenze. Zu diesem Zweck, besonders wenn es dabei zu Brandmarken kommt, benötigen Sie Ausschussteile.
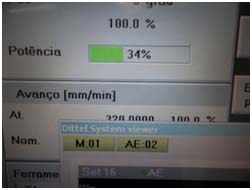
Wenn der Amp-Messer 20% der Höchstlast anzeigt, können Sie den Vorschub schrittweise um jeweils 20% pro Schritt erhöhen. Wenn er 60% anzeigt, 10% pro Schritt. Das Ziel ist immer ein stabiler Prozess. Wir wollen keine Ergebnisse, die anfangs gut aussehen, aber bei Schichtwechsel deutlich nachlassen. Wenn Sie ein Limit erreicht haben, entweder Scheibenaufriss oder Brandmarken, reduzieren Sie den Vorschub um 20%, um die Prozesstabilitätszone zu erhalten.
Was haben Sie beobachtet? Wie hat sich die Scheibe verhalten? Formverlust hat einen der folgenden Gründe:
• Die Scheibe ist zu weich
• Oberflächengeschwindigkeit ist zu niedrig (schrittweise um 3 bis 5 m/s pro Schritt erhöhen)
• Vorschübe sind zu hoch
• Abrichtabtrag ist zu niedrig
• Die Körnung ist zu groß
Führte der Prozess zu Brandmarken?
Prüfen Sie, ob die Scheibe nach dem Abrichten scharf ist. Fühlen Sie hierzu die stillstehende Scheibe mit Ihren Fingerspitzen. Wenn Sie sich glatt anfühlt, müssen Sie Ihre Abrichtparameter nachstellen, oder die Scheibe mit einem Abrichtstein nachschärfen, wenn Sie superabrasive Schleifmittel verwenden. Überprüfen Sie die Kühlung. Ist die Düse in der richtigen Position? Wird der Kühlmittelzufluss durch die Halterung blockiert? Die Oberflächengeschwindigkeit kann zu hoch sein. Versuchen Sie, die Scheibengeschwindigkeit um 3 bis 5 m/s zu reduzieren. Erhöhen Sie den Vorschub, um das Selbstschärfen der Scheibe zu verbessern. Zu diesem Zweck 10% Schritte einsetzen.
Aufzeichnung
Legen Sie Ihr eigenes Arbeitsblatt mit allen Hauptparametern für jeden der Durchgänge zum Schleifen eines Teils an. Diese Parameter müssen aufgezeichnet werden:
- Scheibengeschwindigkeit vc
- Schnittiefe ad
- Vorschub vw
- Materialabtrag Q’w
- Durchschnittliche Spandicke hm
- Aggressivität der Schleifscheibe Fa
- Abrichtverhältnis qd und Abrichtabtrag ad
- Amp-Last in %
- Zykluszeit: tc
Veröffentlichung
Machen Sie Ihren Kollegen diese Ergebnisse zugänglich und legen Sie eine Datenbank an, mit deren Hilfe Sie beim nächsten Test schneller Ergebnisse erhalten.
Mit einem wie hier beschriebenen, systematischen Ansatz kann die Prozessstabilität und –effizienz verbessert werden, und das volle Potential moderner Schleifscheiben voll ausgenutzt werden
Formeln & Abkürzungen
Fa (Aggressivitätsfaktor (20 bis 30)) |
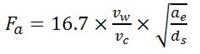 |
Q’w (Q-prime): |
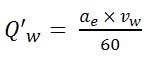 |
hm (durchschnittliche Spandicke): |
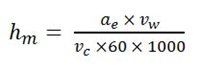 |
vd (Vorschub der Formabrichtrolle) |
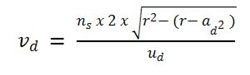 |
qd (Geschwindigkeitsverhältnis beim Abrichten) |
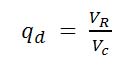 |
qs (Geschwindigkeitsverhältnis beim Schleifen) |
 |
· ad = Schnitttiefe der Abrichter pro Durchgang oder Umdrehung in mm
· ae = Schnitttiefe pro Durchgang in mm
· ds = Schleifscheibendurchmesser in mm
· ns = U/min der Scheibe
· qd = Geschwindigkeitsverhältnis zwischen Scheibe und Abrichtrolle
· tc = Zykluszeit in Sekunden
· ud = Überlappverhältnis der Formabrichtrollen (4 zu 8)
· vc = Scheibenoberflächengeschwindigkeit in m/s
· vd = Vorschub der Formabrichtrolle in mm/min
· VR = Abrichtrollenoberflächengeschwindigkeit in m/s
· vw = Werkstückvorschub in mm/min
Artikel von Walter Graf, Chief Marketing Officer, Winterthur Technology Group 2011
10 Dezember 2011