E-Sharp News
March 2011
TapX - Huge Savings in Tap Production by Scrapping Dedicated Machines
ANCA’s innovations have often turned the cutting tool production market on its head. The TapX may well be the machine to do just that in the tap production market. Taps are traditionally made on a production line of sequential, single operation machines. But as we watched our customers struggle against the inflexibility of these lines in the face of falling batch sizes and demand for greater varieties of taps, we felt compelled to re-invigorate tap grinding with a shot of ANCA’s renowned flexibility and innovation. The result is the TapX; a unique machine, designed to manufacture complete taps in a single set-up and to do so economically, regardless of how unusual the tap is, or how many (or few) you need to produce.
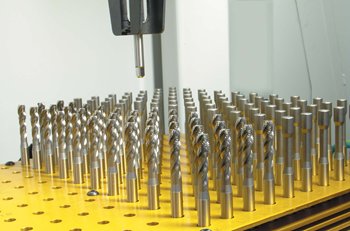
Peter Sutton, of Sutton Tools Australia, describes the allure of grinding special taps. He reports that a HSS tap with non standard geometry can be sold for five to ten times the price of a standard tap; and even higher for a carbide tap. But he adds ‘for such special taps, the batch sizes tend to be smaller. We needed a solution for grinding batches of anywhere from 10 to 250 taps.’
26% Saving on Production of Small Batches of Special Taps

ANCA’s TapX product manager, Duncan Thompson reflects on Sutton Tools’ challenge, ‘we did a complete cost breakdown of the set-up and grinding of a batch of one of Sutton Tools’ special taps (a high helix, HSS M8) on a typical production line and compared it to the TapX. The results are quite remarkable. The savings work out to a theoretical 26% cost reduction per tap for a batch of 50 taps. These days, a 2% cost reduction is significant, but to save a quarter of the cost. Well, that’s why we think the TapX is a game changer’.
In his analysis, Thompson accounted for the obvious costs including, raw materials, consumables, capital amortisation and production time. But digging a bit deeper, he found that the TapX option also offered significant savings in reduced labour costs for set-ups and part transfer as well as savings in less obvious areas such as reduced floor space rental, maintenance costs and less downtime.
Dual Roles – Small Batch Specials and Volume Production
While the cost benefit of TapX decreases as the batch size increases, our modelling shows that it is still economical for very large batches of tools, and there are many other benefits that make it an attractive volume production machine as well. For example, the single clamping nature of the TapX process is inherently more accurate than the re-clamping required in traditional sequential processes. Other valuable benefits accrue when you tool up with multiple TapX machines. Because they can all do the same jobs, you can balance your production load across any available machine and if one machine of four is down, you lose 25% capacity, not the entire production line.
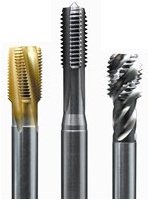
Probably the TapX’s most impressive trait is the flexibility it has as a dual purpose machine for both special and volume orders. Peter Sutton highlighted this fact when we investigated how he was using his TapX in actual production. During the day, Sutton Tools use their TapX to manufacture lots of small batches of high value, special taps like the M8 we have just described. Then in the evening, they load a pallet of blanks into the machine’s auto-loader and leave the machine running overnight, performing unmanned production of large runs of carbide forming taps, or some other high volume order.
Sutton concludes, ‘when we purchase machinery, we have a requisite pay-back period of three years. For our TapX, because of the high value-add we are achieving on the special tools it makes, we will comfortably hit this target.’
Where the Cost Savings are Coming From
In a conventional production line, Sutton Tools’ special M8 tap would be produced on separate machines, one each for; tap flute grinding, tap thread grinding and chamfer grinding. By combining these operations into a single machine, we calculated the typical savings of using a TapX for this job to be:
• 48% lower capital investment in machines
• 56% less set-up time per batch
• 53% less floor space
• reduced utility costs including power, ancillary coolant systems and annual maintenance
As Thompson mentioned, on a batch of 50 taps, these savings work out to a theoretical 26% cost reduction per tap. One of the keys to delivering these huge savings, is the reduced time required to set-up the TapX. Every minute of set-up time costs you twice; firstly the labour cost for an operator to perform the set-up, and second, the lost production time while the machine is not making tools. Now multiply this out for a conventional tap production line including three or four dedicated sequential machines and you start to see the value of single set-up tap grinding on the TapX.
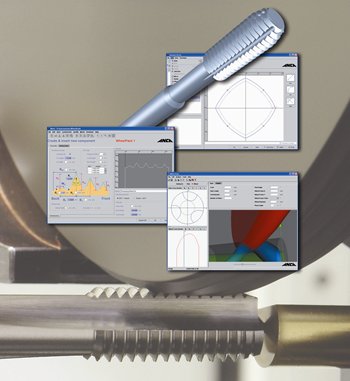
Bearing in mind the pivotal role of quick set-ups in cost reduction, we went to great lengths in designing the TapX to make set-ups especially fast. You can use ANCA’s offline software; CIMulator3D to program and simulate every grinding operation of a new tap, see the cycle times, quote on the batch, and examine the resultant geometry in 3D, without interrupting the machine for a single second. Grinding wheel packs are married to individual coolant manifolds and are assembled offline for instant access when you need them. Tool holding on the headstock and tailstock have been carefully designed to be changed in minutes, and the coolant delivery system can also be quickly adjusted. For batches smaller than 50, ANCA’s attention to quick set-ups on the TapX will have an even more dramatic impact on your profit per tap.
TapX – The Future of Tap Grinding is Single Set-up
It will cost you less money and floor space to tool up and grind highly profitable special taps with a TapX than it would to install a conventional tap production line for low margin standard taps. But with a TapX, you have the flexibility to quickly and easily change from producing special taps to producing cost competitive standard taps, so you win both ways. Yet again, ANCA’s renowned flexibility is proving invaluable in helping you meet the tough production challenges of today. Talk to your local ANCA representative about how a TapX will reshape your tap production process, or help you profitably enter the tap market for the very first time.
Download TapX brochure
23 March 2011