E-Sharp News
March 2011
IMTS 2010 Exhibition, Chicago, USA
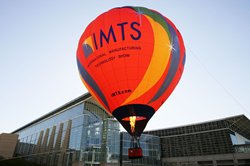
As the premiere machine tool show in the USA, IMTS proved to be the ideal place to introduce ANCA’s newest machine, the TXcell, to the market. The TXcell is a flexible CNC tool grinder with integrated, multifunction robot work cell and is a revolutionary new system designed for efficient cellular tool manufacturing. At IMTS the machine demonstrated ANCA’s new process of BLANKET Grinding where blank carbide rod is manufactured into mixed batches of completed tools in a single set-up, demonstrating the true versatility of the TXcell.
TXcell - developed to meet your business needs
In discussions with tool manufacturing customers, it became clear that their profits were under pressure from a variety of factors. Falling prices, rising costs and the demand for increasingly difficult-to-achieve tolerances all put the squeeze on a business. Many manufacturers had commented that installing a dedicated production line of single process machines, is no longer the answer to achieving maximum manufacturing efficiency.
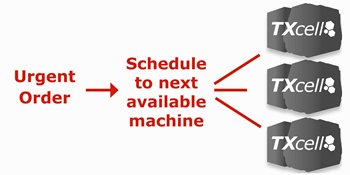
In today’s dynamic world, demands on grinding machines change rapidly. Often just when a dedicated line is beginning to generate realistic profits, the market shifts, creating the need to re-tool. Also, customers are now demanding an ever increasing range of tools, in smaller batches and of higher quality, whilst at the same time insisting on cost savings and quicker deliveries. This increased need for tool makers to become more agile and responsive to their customers’ demands, was the prime motivation in ANCA’s development of the TXcell concept and the BLANKET grinding process.
eXcellent Flexibility
For over 30 years, ANCA’s software has been the industry benchmark for ease-of-use and flexibility. Whether using the inbuilt tool wizards for standard drills and endmills, or diving deep into advanced features like the Special Operations Manager and Program Scripting to create user interfaces for your own unique families of tools, iGrind has been designed with your needs in mind.
TXcell’s integrated robotic work cell takes ANCA’s renowned flexibility to new heights. With up to 24 wheel packs, TXcell combines features to allow you to schedule mixed batches of varying diameter tools. Clever tooling design and software flexibility means zero re-tooling time from one batch to the next.
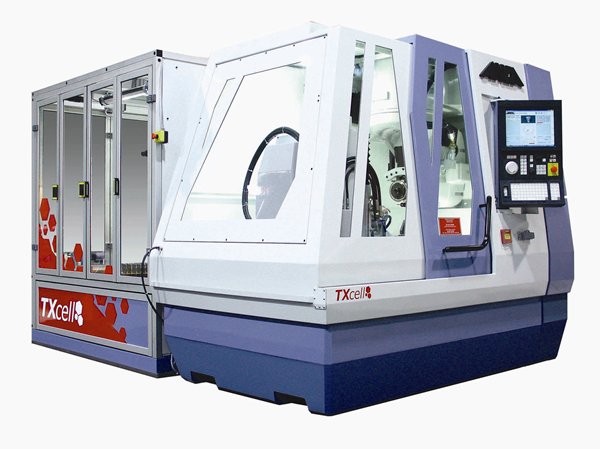
If your production process requires it, TXcell offers the flexibility to include a variety of pre and post grinding operations directly into the cell to suit your individual needs. This directly meets the needs of customers like Duane Gliniecki (Sumitomo Electric Industries – Wisconsin, USA) who comments, “we are continually under pressure to combine processes. Bringing in a process like brush honing into this grinding cell is a great possibility”. Other opportunities include laser etching of tools, deburring, or quality inspection – all depending on your production process needs. And since the robot handles these operations while the machine is busy grinding, that’s money saved, straight to your bottom line.
eXcellent Productivity
You know that if you can increase machine up-time, reduce set-up time and manual interventions and at the same time increase grinding efficiency, these factors will combine to give you a quicker and superior return on your investment. John Leppin II (Garr Tool, Michigan) summed up a problem reiterated by many manufacturers. “We face limitations with the number of machine operators we can get, so anything that can reduce machine down time is an advantage.” John observed “with over 20 wheel packs available on the TXcell, we would look to have simplified wheel pack configurations to avoid interference issues and simplify the set-up. Then if we have repeat sets of those wheel packs, we can do batch runs of over 1000 tools in a single run.”
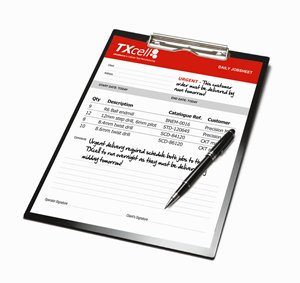
TXcell excels at productivity. It can work through 3 full pallets of tools in a single unmanned run. TXcell’s 37kW (49hp) spindle and wheels of up to 300mm (12”) give you maximum grinding efficiency and wheel life. Two optional NC wheel dressers and automatic white-sticking ensure you maintain wheel form and condition, even across very large batches of tools. Or for very large batches, you can load your TXcell up with duplicate wheels and switch to them, mid batch if you prefer.
But your machine’s not making money for you if you’re wasting time tweaking the set-up for each batch. Re-tooling time between batches can effectively be zero using TXcell’s flexible tooling and scheduling software, but what about programming a new tool? With CIMulator3D, you can program and simulate the entire grinding process offline. On the machine, ANCA’s patented MPG Feed is the fastest and safest prove out technique available anywhere. The optional iView camera lets you measure tools without removing them from the machine, making sure your new tool design is ready for unmanned production in the shortest time possible.
eXcellent Precision
Count the microns! Have you noticed there are less of them on your customers’ tolerance specifications each year? Have you noticed the higher prices that ultra-accurate tools command and want a bigger slice of that pie? Certain things are vital if you want to reliably produce accurate tools. You need a stable machine and process, accurate wheels and accurate tool holding.
Based on ANCA’s highly respected TX7+ platform, TXcell’s rigid gantry design, vibration dampening ANCrete base and direct drive technology is perfectly accompanied by touch or laser probing and software compensation options for statistical process control (SPC) and temperature variation compensation (CTV). So you know that process stability is assured.
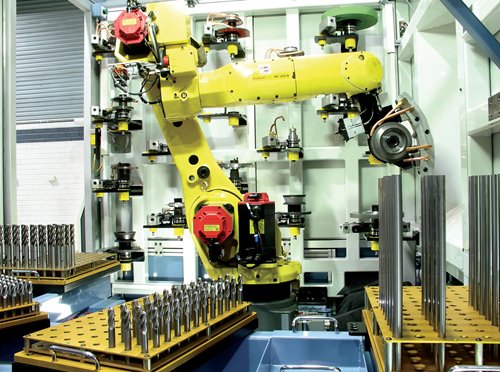
Excessive wheel run out is now a thing of the past with TXcell. NC controlled spindle orientation ensures that each wheel change occurs with perfect angular re-alignment. Onboard dressing and the ANCA iBalance system will keep your wheels running fast and true.
Multiple tool holding options help you eliminate run out and profile errors from your tools. The NC controlled P-axis steady can be tooled up with bush, tailstock or an Arobotech, auto-centering tool support system for added stability.
BLANKET Grinding elegantly demonstrates the TXcell’s benefits and capabilities
Blanket Grinding is a new process approach to tool production, where all tool manufacturing operations from BLANK stock to finished TOOL are achieved within a single manufacturing cell. This eliminates the need for separate sequential machines and processes traditionally required for the complete tool manufacturing process. This in turn brings benefits by reducing capital investment costs, factory floor space requirements, inventory stock and most importantly labour for manual handling and machine set-up.
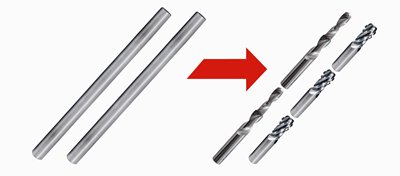
Bar stock to finished tools in a single set-up!
At IMTS, sequential processes of blank parting, shank chamfer grinding, cone point grinding, step cylindrical grinding and back taper peel grinding were all performed on the TXcell before the final tool grinding was done. Even more impressively, this cell was producing three different types of tools within the one set-up.
Can you see Cellular Tool Manufacturing in your future? Or would you rather struggle with the profit squeeze and leave it for your competitors to explore? Contact your nearest ANCA representative to find out how TXcell can change your future tool manufacturing today!
15 March 2011