E-Sharp News
September 2011
Jeffrey A. Badger, Ph.D.
The Grinding Doc Consulting
Austin, Texas USA
www.TheGrindingDoc.com
JB@TheGrindingDoc.com
Finding the “Sweet Spot” of your wheel
Every grinding operation has a “sweet spot”. When you’re in the sweet spot, the speeds and feeds are set just right and the wheel cuts well, gives a good surface finish, doesn’t wear away too quickly, and generally just grinds better. When you’re not in the sweet spot, all types of problems can occur: the workpiece burns, you get chatter, or the wheel just wears away very quickly. Finding this sweet spot is extremely important for efficient, low-temperature grinding.
In production grinding, machine operators are usually pretty good at finding this sweet spot. Over time, they tweak their feedrates and wheel speeds to find a set of parameters that work well for the given wheel, workpiece, coolant and grinding machine combination.
But what happens if the operator is assigned a new job? Let’s say he’s grinding carbide endmills, and instead of grinding the usual 6-mm-diameter endmills he’s assigned the task of grinding 25-mm-diameter endmills, with a much larger depth of cut. What does he do then? Well, he’ll just have to repeat the whole tweaking operation again to find the sweet spot.
Is there a better way than this trial and error method? The answer is a definite YES! Instead of thinking in terms of speeds and feeds, think in terms of Aggressiveness. For the 6-mm-diameter job, the operator found an Aggressiveness that worked well for that wheel, workpiece, coolant and machine combination. He now needs to repeat that Aggressiveness for the new job.
What is Aggressiveness?
Aggressiveness is simply, how hard we’re pushing the grits in the wheel. It’s similar to penetration depth or chip thickness, as shown in the following diagram. If the Aggressiveness is too large, the grits penetrate deep into the material, the forces on the grits are too large and the grits get ripped out of the bond material prematurely. If the Aggressiveness is too small, the grits just tickle the surface, there’s a lot of rubbing and heat generation, and the forces are not large enough to get the grits to self-sharpen – they just dull. In between these two extremes lies the optimum Aggressiveness – or the sweet-spot.
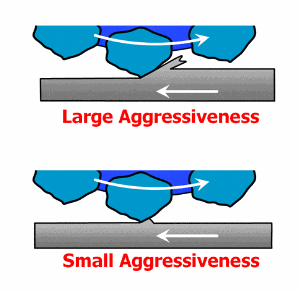
The Aggressiveness Number is related to how deep each grit penetrates into the workpiece
Calculating Aggressiveness
The Aggressiveness Number is calculated by the formula below:

Here we see that a larger workpiece speed, or feedrate, gives a higher Aggressiveness, as does a deeper depth of cut. A faster wheel speed reduces the Aggressiveness, as a fast wheel speed means the grits don’t penetrate as deeply; a larger wheel diameter gives a lower Aggressiveness.
Good Numbers
What is a good Aggressiveness Number? That depends on the particular wheel and the type of material being ground. Each wheel/workpiece combination has its own narrow range of Aggressiveness Number that puts it in the sweet spot. If your operator has been tweaking the job for a while, chances are he’s found a good Aggressiveness Number for that operation. Once he has it, stick with it.
The Blind Men and the Elephant
I recently visited a company that was grinding tungsten-carbide endmills with a particular resin-bonded diamond grinding wheel. There were two operators, Joe and Hank, running similar jobs on the same machine with the same wheel specification. Joe swore that his parameters were the best for the job. Hank had a different opinion: that his parameters were best.
I then got on the Internet and found the brochure from the grinding-wheel manufacturer with their case-study for the wheel. Their parameters, along with Joe and Hank's are given in the table below:
|
Depth of cut (mm)
|
Feedrate
(mm/min)
|
Wheel speed
(m/s)
|
Wheel
diameter
(mm)
|
Material-removal
rate
(mm3/mm/s)
|
Aggressiveness Number |
Joe's Parameters for
small-diameter
carbide endmill
|
2.5 |
150 |
18.5 |
150 |
6.3 |
17.4 |
Hank's Parameters for
medium-diameter
carbide endmill
|
2.9 |
115 |
16.5 |
120 |
5.6 |
18.1 |
Brochure on wheel from wheel manufacturer - Case study:
Grinding of medium-diameter
carbide endmill
|
2 |
300 |
33 |
150 |
10.0 |
17.5 |
Grinding parameters, rough-grinding of tungsten-carbide with diamond wheel
Looking at the parameters, we see that Joe was running at 18.5 m/s and Hank was running at 16.5 m/s. I asked Joe what he thought of Hank’s parameters and he said, “No way. Hank doesn’t know what he’s doing. If I run at 16.5 m/s I chew the hell out of my wheel and I get chipping at the exit point.”
I then asked Hank what he thought. Hank said, “Joe’s crazy. If I run at 18.5 m/s, I’ll glaze up my wheel and crack my parts.”
I then asked both of them what they thought of the wheel-manufacturer’s case-study parameters. They both balked. “Ridiculous”, they said. “33 m/s is absurd.” At least they agreed on something.
However, let’s look at the Aggressiveness Numbers. Here we see values of 17.4, 18.1 and 17.5. These are all pretty close to each other in spite of the radically different wheel speeds. Why? This wheel specification liked to be run at an Aggressiveness of around 17.5 to 18.0. This can be achieved in numerous ways – and was. Each operator, including the guy at the wheel manufacturer, did his own tweaking and arrived at pretty much the same Aggressiveness Number.
Use it to your advantage
So next time you're on a machine, calculate the Aggressiveness Number. Over time, develop a database of Aggressiveness Numbers that work well for a given process. Once you have the Aggressiveness Number that gives you the sweet spot for a wheel, make a note of it. Now, let’s say you have a smaller part size and have to decrease the depth of cut. That’s fine. Just choose a feedrate and wheel speed that gives you the same Aggressiveness Number. That will quickly put you back in the sweet spot for that wheel.
I first developed the concept of Aggressiveness in 2001 and began teaching it at my High Intensity Grinding Course in 2007. When I talk to past course attendees many of them say the same thing: “You know, the thing I learned in the course that we use all the time is the Aggressiveness. Whenever we had a problem, we’d check our Aggressiveness Number to see if it jibes with what we typically use. And whenever we had a problem, our Aggressiveness Number was almost always too low or too high. We now monitor our Aggressiveness Values all the time and it helps keep things in line.”
So stop thinking about speeds and feeds. Think Aggressiveness.
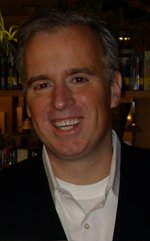
About The Author
Dr. Jeffrey Badger is an expert in grinding and an independent consultant. He will be giving his three-day High Intensity Grinding Course 19-21 October in Columbus, Ohio, USA, hosted by Diamond Innovations. He'll also be making the rounds at EMO. Visit www.TheGrindingDoc.com for details on the course or to schedule a visit at EMO.
12 September 2011