ニュースレターを発行
2024年3月
多くの切削工具を使用している人も、時には適切な工具がどうしても見つからないという人も、おそらく自作を検討したことがあるだろう。少なくとも、使い古した工具を研ぐことは。しかし、工具研削を社内で行うことが賢明な決断かどうかは、どのように判断すればよいのでしょうか?GKNエアロスペース・エンジンが直面したこの疑問について、主席製造エンジニアのジェレミー・サンピエールがその考察を説明してくれました。さらに、内製化に踏み切った場合のベストプラクティスについて、貴重なアドバイスも提供しています。
コスト削減により2年で投資回収
CNC工具研削盤と必要な付帯設備は、大きな投資となります。そこでGKN社の経営陣はSt.Pierreに、工具の消費量を調査し、工具研削を内製化することで達成できる節約の可能性を予測するよう依頼しました。St.Pierre氏は、同社の工具の多くが何度も再研磨可能であることが重要な要因の一つであると説明した。例えば、サン・ピエール氏は、同社の多くのテーパー・ボールノーズ・エンドミルを例に挙げ、これらの工具は "毎回、真の形 "に研ぎ直すことができると指摘した。
逆に、サンピエール氏は、これらの工具の多くは、不等間隔割り出しや可変ヘリカルなど複雑であるため、多くの外部ベンダーは、元々その工具を製造していない限り、再研磨を行いたがらない、と注意を促した。そのため、自社で再研磨できなければ、限られた供給量に縛られることになり、コストと潜在的なリスクを伴うことになる。
サンピエールはまた、大量生産される工具の中には、業界の標準品でないために非常に高価なものもあることに気づいた。「ハーフインチカッターの代わりに、直径0.485インチのカッターを使うこともあります。これは技術的にカスタムメイドなので、割高な料金を支払って12週間分の工具を注文していました。リードタイムも長かった サンピエールは、「良い価格を得るために一度に70本の工具を送らなければならない」頻度も含めて、工具にかかる真のコストを計算することで、ANCA MX7リニア工具研削盤4台、ZOLLER「タイタン」測定機、砥石ドレッサーやドラッグフィニッシャーなどのサポート機器一式を備えた、当初想定していたよりもさらに高性能な工具室に投資することを強く主張することができた。しかし、投資回収期間はわずか2年でした。
とはいえ、サンピエールはGKNが工具に莫大な費用を費やした大企業であることを認識している。彼はまた、"すべてを導入できる "と言う前に、"簡単な勝利"、つまり重要かつ実行可能なツールをよく見ることを提案した。そうすれば、自信を持ってグラインダーと関連ギアを指定し、数字がうまくいくかどうかを確認することができる。
より速いターンアラウンド
サンピエールのツールルームは、生産現場が必要とする工具を迅速に提供するだけで、GKNの全体的な効率を大幅に向上させます。また、再研磨だけではありません。「現在、直径8分の1インチから8分の1インチまで、切削長5.5インチのあらゆる工具の研削にANCAマシンを使用しています」とサンピエール氏は説明します。「単発の特注工具や、緊急修理が必要な場合にも対応しています。複合材用工具、特殊素材用工具、プラスチック用工具、木材用工具...必要なものは何でも作ります」。カスタム・ツールのリードタイムは最短で1日、最長で2週間という。「そして、1つだけ欲しいのであれば、1つだけお作りします」。
加工を改善するために設計を微調整する
社内の研磨工場では、専門メーカーよりも優れた切削工具は作れないと思うかもしれない。しかし、GKNに集中し、サン・ピエールが積極的に実験に取り組んでいるおかげで、チームは実際、「他の超有名工具メーカーの工具にかなり勝っている」とサン・ピエールは言う。「それが私たちの意図というわけではありません。ただ、私たちのオペレーションと製品に集中し、その生産環境に合わせて工具をカスタマイズすることができるのです。私たちには、私たちのためだけにツールを微調整する能力があるのです」。
サン・ピエールは、彼のアプローチを "壊れるまでやり続け、そして最高のツールを作るために調整する "と要約している。休止中の機械があれば、GKNの付属工場で工具を試したり、専用のテスト機があり、すぐにフィードバックが得られるスウェーデンの拠点に工具を送ったりする。また、長年一緒に仕事をしてきた企業にもサンプルツールを渡し、意見を求めることもある。
サン・ピエールはまた、ANCA(本拠地ミシガン州ウィクソム)が工具設計の課題を解決してくれたことも評価している。「年に数回、ミシガンに行きます。苦労しているときは、たいていANCAにあまり人が作っていないような工具を渡して、一緒に座って設計してもらうんだ。あるいは、彼らが私に電話をかけてきて、電話でそれをやる。1日か2日以内に、一緒に道具を作る。彼らは何も求めない。どうなっているか知りたいだけなんだ。とても助かっているよ
サン・ピエールが報告した驚くべき発見のひとつは、OTECドラッグ仕上げ機で刃先をホーニングすることで、多くの工具にコーティングを施す必要がなくなったことだ。「サンピエール氏は、「私たちの工具は、コーティングを施したものよりも、刃先の前処理を施したものの方が長持ちします。「高温加工に使用する場合は、多くの工具をコーティングしています。しかし、私たちは "チタン "イウム用のテーパーボールを多く製造しており、多くのテストを行ってきました。工具の端面を整えるだけで、長持ちするんだ。以前の工具の4倍の寿命になったこともあります」。
より高い性能に加えて、サンピエールは、エッジプリッピングによって、コーティングに必要なおよそ1週間のリードタイムが不要になり、さらにそのコストと余分な輸送とハンドリングも不要になると付け加えた。「再研磨のコストは5ドルかもしれないし、100ドルかもしれない。「しかし、5ドルの再研磨なら、10ドルのコーティングになります。これで、基本的に工具コストの3倍になります。しかし、5ドルの再研磨でも10ドルのコーティングです。(サンピエールによれば、GKN社の平均ホーニング時間は約1分で、OTECは一度に25本の工具を加工する)
独立したプロフィットセンター
サン・ピエール氏のツールルームは、コネチカット州ニューイントンにあるGKNの航空宇宙エンジン工場に併設されているが、独立したプロフィットセンターとして運営されている。北米にある7つのGKNエアロスペースエンジン拠点すべてにサービスを提供し、さらに地元の他の航空宇宙企業にも工具を販売している。また、他の航空宇宙関連企業にも工具を販売している。GKN社にとっては副次的なことだが、社内で工具研削を行うことを決定する際には、この可能性も考慮する価値がある。
適切な研削盤の選択
工具研削に踏み切る準備ができたら、次に最も重要な検討事項は、どの工具研削盤に投資するかということだ。当然のことながら、使いやすさとサポートは重要な要素であり、機械メーカーの枠を超えて考えることが賢明です。現在使用しているサプライヤーに、どのような機械を使用しているのか、また、プログラムの共有やその他のサポートを提供してくれるかどうかを尋ねてみてください。GKN社にとって、ANCA社は明確な選択でした。なぜなら、ANCA社はマーケットリーダーであり、スウェーデンの事業所にはANCA社の機械があったからです。
「そうすれば、お互いに助け合うことができます。「私たちはお互いにプログラムを送り合うことができ、同じように研削することができます。工具の製作が必要な場合は、プログラムを送ってもらい、工具を加工して送り返すことができます。
サン・ピエールがGKNでプロジェクトを始めたとき、製造と問題解決の経験は何年もあったが、工具を研磨したことはなかったことを強調しておきたい。それは、その後チームに加わった全員についても同様である。「機械に詳しく、現実の世界を理解し、物事を複雑にしすぎてはいけないとわかっている人を採用しました」とサンピエールは語る。「最初はみんな緊張していたけれど、最初にやったことは、ミシガン州に飛んでANCAで2週間のトレーニングを受けることだった。それから走り始めたんだ」。それ以来、彼らは学び続け、何度か失敗もした。しかし、失敗したツールは一度しかない。
サンピエールは、ANCAのソフトウェアを絶賛した。「自動化する際の再キャリブレーション、再運転、ポジションの再教育など、彼らのものはすべて、本当に順を追って説明してくれます。今まで使った中で最も使いやすいマシンだ。この機械を見たことがない人をフロアから連れてきても、30分以内に工具を作ることができる。機械上で設計し、何をやっているのかわからずに研削することもできる」。
適切な測定機
工具室、特に航空宇宙企業にとって、2番目に重要な投資決定は検査設備である。ミシガン州アナーバーに本社を置くZOLLER社もまた、自然にフィットした。第一に、GKNはすでにZOLLERのプリセッタを持っており、サンピエールは彼らが築いた円滑な協力関係を高く評価した。第二に、ZOLLERはANCAと緊密なパートナーシップを築いており、その結果、両社の機械の能力を高めるソリューションが生まれた。そのため、GKN社は、フルート形状や刃先処理など、あらゆる工具属性を光学的に自動測定できるZOLLERの最上位機種「titan」を選択しました。
高精度の自動化
GKN社はすべてのANCA MX7工具研削盤にロボットローダーを追加し、砥石ドレスと測定も内蔵しました。この機械には、工具プロファイルをスキャンし、研削プログラムを自動的に補正して、公称形状からのずれを修正するレーザーも内蔵されています。これらの機能により、無人のシフトでも公差の厳しい工具を生産することができます。「私たちは、工具の公差をプラスゼロとマイナス5分の1に抑えています。「とサン・ピエールは言う。仕上げ加工用のボールノーズであれば、コンマ数秒を維持します」。
ZOLLER "titan "にはロボットローダーもあり、ZOLLERはこれを "roboSet2 "と呼んでいます。さらに、4台の研削盤と測定機は消灯中に自動的に工具径を変更できる。これは重要なことだとサンピエールは説明する。というのも、同社は「GKN向けに400もの異なる部品番号を製造している」からだ。1000個のバッチではなく、15~20個のバッチを作っているのです」。そして、ごく少数の例外を除いて、全工具の10~100%を検査しなければならない。そのため、ボトルネックを防ぐためには、柔軟なワーク保持が不可欠です」。
どちらのシステムも、中間スリーブの挿入で異なる直径をクランプするシュンク社の油圧チャックを使用している。GKNの場合は、ロボットがスリーブを交換する。サン・ピエールはこう説明する: 「roboSet(またはMX7ローダー)には、すでにすべてのスリーブが内蔵されており、どこに何があるかを把握しています。例えば、バッチ番号1がハーフインチの工具だとします。ロボットはハーフインチスリーブを掴んでチャックにセットします。そして、そのハーフインチツールをすべて稼働させ、必要な報告を行います。それが終わると、スリーブを交換し、次のサイズのツールをつかみ、そのプログラムの実行を開始します。プログラムを書いて、スケジュールを選択するだけです」。GKNは5つの異なるサイズを収納できるようにパレットをカスタマイズしており、サンピエールは1回の無人シフトで20種類の工具設計をZOLLERに通すことができると述べています。
GKN社はANCAツーリング・ソフトウェアを使用して、「業界が慣れ親しんでいるダミー・ソリッドではなく」、非常に詳細な工具のプリントを作成しています。「そのため、実際の工具とその設計方法のすべてのパラメーターを含めることができます」。これらのプリントは検査ルーチンを決定する。「標準的な工具では、22から30の異なるパラメータを調べます。しかし、私たちは可変インデックス、可変らせん工具をたくさん作っているので、特にセットアップでは、すべてのフルートをチェックする必要があります」。サンピエールは、完全で詳細な検査には「10分かかるかもしれませんが、プログラムをカスタマイズすれば、特定の機能のサブセットを検査するのに1分以内に終わらせることができます」と付け加えた。
ANCAとZOLLERのパートナーシップ
QC要件を満たすために、GKN社は「タイタン」級の独立型測定機を必要としている。しかし、ANCAの測定能力とZOLLERの測定能力がいかに重複しているかに注目してください。両者のタスクをどのように分担するのか?機械は協力できるのか?サンピエールにとって、要求される工具品質を達成すること以外に、生産性を最大化することが目標です。そのため、例えば、オペレーターがいる場合、ANCAの内蔵レーザーを使うよりも、「titan」マシンを使って工具プロファイルをスキャンし、必要な補正データを研削盤に送ることを好む。これにより、MXの工具研削は維持される。
St.Pierre氏はまた、オペレーターが調整方法に迷うような状況についても言及した。「ZOLLERを使って測定し、それを研削プログラムに送って修正します。ZOLLERを使って測定し、研削プログラムに送って修正します。ZOLLERと研削プログラムは簡単に会話できるのがいいですし、セットアップもそれほど難しくありませんでした。そのため、ZOLLERに手伝ってもらいました。"
GKNは研削砥石の測定にもZOLLERを使い始めており、これもMXの生産性を最大化しています。「ZOLLERですべての砥石測定を行うための設備を導入しているので、バッチ全体をセットアップし、データを研削盤に流し込むことができます」とサンピエール氏。
GKNは、オフラインでホイールのコンディショニングを行うスタンドアローンのホイールドレッサーも所有している。しかし、前述したように、無人のシフトであれば、MX機は加工中の工具の研削と測定、さらに砥石の測定とドレッシングの両方を行うことができます。一方、ZOLLERは以前に研削された工具の完成品検査を行う。
その他の付帯設備
どんな工具研削工場でもクーラント濾過と温度制御が必要で、GKNではダブルベッセル・トランサーシステムで対応しています。カットオフマシンは、超硬ブランクのサイジングにも便利です。ここでGKN社は独創的なアプローチを取り、マキノのU6ワイヤーEDMを選択した。サンピエールが言うように、「カットオフしかできない機械にそれだけの出費を正当化できるほど、価格差は大きくありませんでした。そこで、大ロットでカスタム切断を行うためにワイヤーEDMを購入しました。また、会社全体の固定具と検査ゲージも自作しています。その機械は、研削工具とは関係ないものを作っていた最初の年に元が取れました」。サン・ピエール氏は、EDMを使って工具プロファイルを切削し、ANCAでフルートと外径を研削することもあると付け加えた。「私たちはEDMで研削公差を保持することができます。EDMはすでにANCA用のステディレストブッシュの製造に使用しています。
ZOLLERのTMS工具管理ソフトウェア、ロボットグリッパーやその他の工具用の3Dプリンター、Modula VLM保管タワー、レーザーマーカーを加えれば、GKNの工具室が効率的であると同時に自給自足的であることが分かるだろう。
それは「大変な作業」であり、大きな投資だった。しかし、サン・ピエールはこうまとめている: 「このプロジェクトを見て、悪い投資だったとは誰も言わない。誰もがもっと早くやっておけばよかったと言っている。"
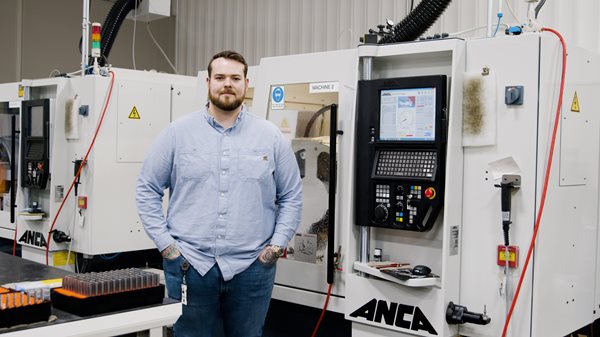
ジェレミー・サンピエールは、GKNエアロスペースエンジンの社内工具研削工程を立ち上げ、わずか2年で元を取った(画像提供:ZOLLER)。
6 3月 2024