E-Sharp News
June 2011
Microns count in any grinding business. Every step you take to improve the accuracy of your product keeps you a step ahead of your competitors, and helps to keep your customers coming back. Buying a new machine is one way to achieve this goal, but may not be a practical short term solution. A much quicker and cheaper alternative can be to upgrade your machine with newer software or tooling.
One such retrofittable improvement being offered for ANCA TX7+ machines is Automatic Spindle to Arbor Orientation. This new development has proven to dramatically improve process stability by maintaining constant relative positions of the arbour to the spindle between successive automatic wheel pack changes.
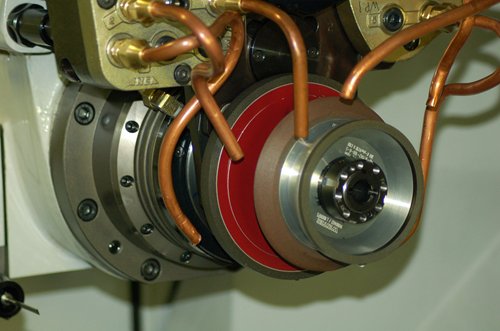
TX7 spindle and wheel pack
Improve Accuracy and Reduce Vibration on Your Existing TX7+
Since its introduction to the market, the TX7+ included automatic wheel pack changing which provides unhindered access to both wheel packs. Whilst the TX7’s BigPlus face and taper contact system ensures industry best results for arbour run-out. ANCA engineers realised that even the smallest inaccuracy in the BigPlus arbor, or it’s mating spindle taper, could have an influence on the actual wheel run-out. ANCA therefore developed a simple system to directly address this issue.
In a perfect world, both spindles and wheel arbor tapers would be manufactured with zero run out. In reality, each will have a small amount of run out resulting from the manufacturing process. Imagine both a spindle and a wheel arbor each with 2 microns run out. When the wheel arbor and spindle are brought together, depending on their relative orientation, the combined run out of the system can vary between 0 microns (run outs subtracted from each other) and 4 microns (run outs added to each other). This in itself is not a problem, because dressing the wheel in place will effectively remove any wheel run out. However, if the system undergoes a wheel pack change, a common operation in running a TX7+, then the relative positions of the spindle and arbor will change, thereby introducing run-out back into the grinding wheel when it is reloaded.
This variation in wheel run out can have a number of undesirable side effects. These include:
- Variation of the effective grinding size of the wheel, directly impacting tool geometry and process stability. E.g. an eccentric OD grinding operation with up to 4 microns variation in the relative grinding diameter of the wheel, would translate to a 4 microns variation in tool radius, or 8 microns on tool diameter.
- Variation of wheel balance, affecting surface finish.
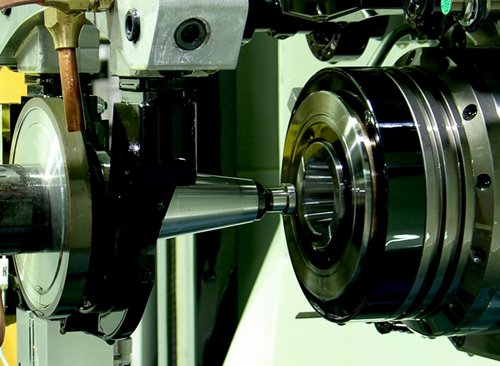
Wheel arbor being mounted into the spindle
ANCA’s Spindle Orientation Solution, retrofittable to your TX7+
ANCA’s Spindle Orientation System includes a specially fitted encoder on the spindle and ANCA’s newly developed spindle drive control technology to ensure the spindle and wheel arbor are repeatedly returned to the same relative positions every time a wheel pack is automatically changed. With less than 1 day of down time of your machine, the Spindle Orientation System can be fitted and running on your TX7+, and you can be enjoying the benefits of a step up in process consistency and grinding results.
10 June 2011