E-Sharp News
June 2024
It began with an accident. Dr. Salah Huwais, a renowned periodontist with several offices in Michigan, USA, started to drill a hole in a patient’s jaw, but an assistant had mistakenly set the hand tool to rotate counterclockwise. Although Dr. Huwais found it hard to push the burr into the bone, he also noticed that trying to do so had the effect of hardening the bone a bit. This gave him the idea that the right tool geometry might be able to both make the required hole and compact the cut bone back into the jaw. If so, this would revolutionize dental implant procedures by greatly reducing the required time to heal.
That was back in early 2014. By April of that year, Dr. Huwais, who had no manufacturing experience, formed the company Versah, LLC, in Jackson, Michigan, and partnered with engineers to turn his idea into reality. It wasn’t easy. Aaron Beach, director of manufacturing and product development, recounted that they went through more than 60 prototypes over 6 months before settling on a design. The resulting dental burr, which is protected by numerous patents, returns all the bone back into the jaw as the periodontist cuts the hole needed for the planned implant. According Beach, this usually enables the surgeon to immediately place the permanent implant, versus waiting 6 to 12 months for the bone to heal, as is required when using a traditional burr.
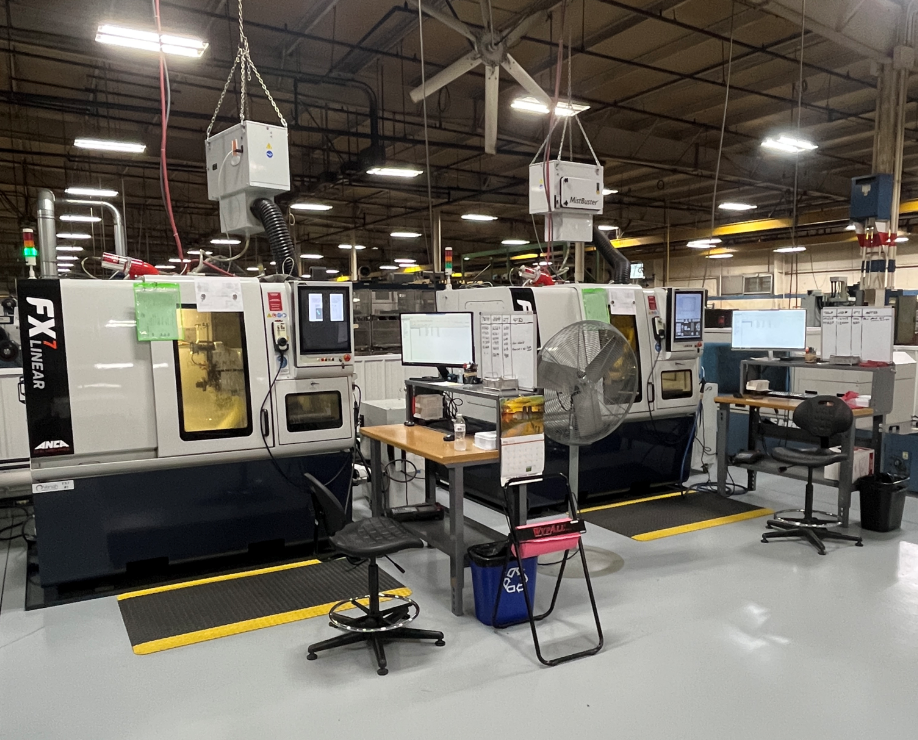
Versah relies on fully automated ANCA machines to grind their complex geometries to tight tolerances over long production runs
ANCA machines are key
Naturally, Versah does not want to publicize all the secrets that go into making these stainless steel tools, except to say that they are ground to “extremely tight tolerances” on ANCA MX and FX machines, where the biggest challenge is accounting for wear in the steadyrest and the grinding wheels, said Beach. But the CBN wheels hold up well enough that they don’t require in-process dressing, he reported. In terms of workholding and part handling, all jobs are fully automated, with a typical batch size of 1,000 burrs.
Beach did reveal that the tools have “multiple geometries” that change throughout the flute, which the ANCA software and machines handle well. Likewise, measuring the geometry is a challenge, the details of which can’t be shared. But Beach said they “inspect parts with a vision system every 30 minutes, and document the inspections every 2 hours, to maintain quality.”
Another important point Beach made is that although he had manufacturing knowledge when starting this project in 2014, he had no grinding experience. Versah jumped in with a fully equipped ANCA MX5 and then a number of FX machines. As Beach recalled, “I did some Solidworks programming in the past that helped. But I didn’t know anything about ANCA’s iGrind software or anything related to grinding. The fact that you’re able to watch the part unfold in the software, to watch the changes happen right in front of you on the machine, makes it very, very user friendly.
“The software is also educational. New people coming in, or even our team in the offices with no manufacturing background, can click on different items, leave some highlighted, and it walks them through how that part’s being ground, and shows how each part of the program is connected with each tool feature. It’s really simple. I have hired a few people on these grinders that had zero experience with them and they’ve picked it up quickly.” Beach also lauded ANCA’s customer service and reliability. “We run these machines around the clock, six to seven days a week. So, they’ve gotten a lot of use, which obviously calls for maintenance and support. But we find them to be very low maintenance.”
Production details
Versah makes their burrs in two lengths and a variety of cutting diameters, but with a single shank diameter that meets the relevant ISO standard. This simplifies their setups, said Beach, such that they use only two collet types. For the longer burrs, the collet swallows more of the shank, providing more rigidity for the grind. They also use a fixed steadyrest on each tool, changing its position based on the tool length. But given Versah’s lot sizes, these adjustments are infrequent.
Versah electro-polishes the tools coming off the ANCA grinder, added Beach, “to remove any free iron. Then they are coated with titanium nitride.” Beach explained that heat reduction is the main coating benefit, since heating the bone typically damages it. “We found that adding this coating, along with the appropriate irrigation, keeps our burrs a little cooler than they otherwise would be. We think the coating also helps prevent the bone from sticking to the burr, and therefore helps transfer the bone back to the jaw.”
On the other hand, the unique geometry is clearly the critical factor, because Versah only added the coating in 2019. By then, the burrs had become a worldwide success. A gratifying success story in improving thousands of lives.
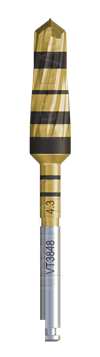
Versah’s patented dental burr enables the surgeon to immediately place the permanent implant, versus waiting 6 to 12 months for the bone to heal, as is required when using a traditional burr
5 March 2024