Lettre d'information "The Sharp-E"
Mars 2024
Que vous utilisiez beaucoup d'outils de coupe ou que vous soyez parfois désespérément à la recherche du bon outil, vous avez probablement envisagé de fabriquer le vôtre. Ou au moins à affûter vos outils usés. Mais comment décider si l'affûtage d'outils en interne est une décision judicieuse ? C'est une question à laquelle GKN Aerospace Engine a été confronté, et Jeremy St. Pierre, ingénieur principal de fabrication, nous fait part de ses réflexions. En outre, il donne des conseils précieux sur les meilleures pratiques à adopter si vous décidez de franchir le pas.
Les économies réalisées permettent un retour sur investissement en deux ans
Les affûteuses d'outils à commande numérique et les équipements auxiliaires requis représentent un investissement important. La direction de GKN a donc demandé à M. St. Pierre d'étudier sa consommation d'outils et de prévoir les économies potentielles qu'elle pourrait réaliser en internalisant l'affûtage des outils. L'un des facteurs clés, explique M. St. Pierre, est le fait que nombre de leurs outils peuvent être réaffûtés plusieurs fois. Par exemple, il a cité les nombreuses fraises coniques à bec sphérique, qui peuvent être affûtées pour obtenir la "forme réelle souhaitée, à chaque fois".
À l'inverse, M. St-Pierre a fait remarquer que nombre de ces outils sont complexes, avec un indexage inégal et des hélices variables, de sorte que de nombreux fournisseurs extérieurs ne veulent pas réaffûter ces outils à moins qu'ils ne les aient fabriqués à l'origine. Par conséquent, si vous ne pouvez pas les réaffûter vous-même, vous vous retrouvez avec un approvisionnement limité, ce qui est coûteux et potentiellement risqué.
M. St. Pierre a également constaté que certains de ses outils à grand volume étaient très coûteux, simplement parce qu'ils n'étaient pas standard dans l'industrie. "Au lieu d'avoir une fraise d'un demi-pouce, nous pourrions avoir une fraise d'un diamètre de 0,485 pouce. Comme il s'agit techniquement d'un produit sur mesure, nous payions un supplément et commandions 12 semaines d'outillage. Et nous avions de longs délais de livraison". En calculant le coût réel de l'outillage, y compris la fréquence à laquelle il fallait "envoyer 70 outils en même temps pour obtenir un bon prix", M. St-Pierre a pu justifier l'investissement dans une salle d'outils encore plus performante que celle envisagée à l'origine, avec 4 affûteuses d'outils linéaires ANCA MX7, une machine à mesurer ZOLLER "titan" et un ensemble complet d'équipements de soutien tels qu'un dresseur de meules et un finisseur par traînage. Pourtant, le temps de retour sur investissement s'est avéré n'être que de deux ans.
Cela dit, M. St-Pierre reconnaît que GKN est une grande entreprise qui a dépensé une fortune en outils, et qu'il est donc plus judicieux pour de nombreuses entreprises de commencer par une entreprise plus petite. Il suggère également d'examiner de près les "gains faciles", les outils qui sont à la fois importants et réalisables, "avant de dire : 'Nous pouvons tout apporter'". Vous pouvez alors spécifier en toute confiance la meuleuse et le matériel associé et voir si les chiffres fonctionnent.
Un délai d'exécution plus court
L'atelier d'outillage de Saint-Pierre améliore considérablement l'efficacité globale de GKN, simplement en fournissant rapidement les outils dont l'atelier de production a besoin. Et il ne s'agit pas seulement de réaffûtages. "Nous utilisons actuellement les machines ANCA pour affûter des outils d'un diamètre d'un huitième de pouce jusqu'à un diamètre d'un pouce sur huit, avec une longueur de coupe de cinq pouces et demi", explique M. St. "Nous réalisons beaucoup d'outillages personnalisés et de réparations d'urgence... Nous fabriquons tous les outils qui peuvent être fabriqués à l'extérieur. Nous fabriquons des outils composites, des outils pour matériaux spéciaux, des outils pour le plastique, le bois... tout ce dont nous avons besoin". Les délais de livraison pour les outils sur mesure sont d'un jour seulement, ajoute-t-il, et de deux semaines au maximum. "Et si vous n'en voulez qu'un, nous le fabriquons.
Modifier les conceptions pour améliorer l'usinage
On pourrait penser qu'un atelier d'affûtage interne ne pourrait pas fabriquer de meilleurs outils de coupe que les fabricants spécialisés. Mais en raison de la priorité accordée à GKN et de la volonté d'expérimentation de M. St-Pierre, l'équipe a en fait "battu une bonne partie des outils d'autres fabricants d'outils très connus", explique M. St-Pierre. "Ce n'est pas notre intention. C'est simplement que nous sommes en mesure de nous concentrer sur nos opérations et nos produits et de personnaliser un outil pour cet environnement de production. Nous avons la possibilité d'adapter l'outillage à nos besoins".
M. St-Pierre résume son approche en disant qu'il faut "pousser les choses jusqu'à ce qu'elles se cassent, puis les réduire pour obtenir le meilleur outil possible". Ils essaient les outils dans l'usine GKN attenante s'il y a des machines à l'arrêt, ou les envoient sur leur site suédois, où ils disposent d'une machine d'essai dédiée et peuvent fournir un retour d'information immédiat. Ils donnent également des échantillons d'outils aux entreprises avec lesquelles ils ont travaillé au fil des ans et leur demandent leur avis.
M. St. Pierre reconnaît également que l'ANCA (basée à Wixom, MI) l'a aidé à relever certains de ses défis en matière de conception d'outils. "Je me rends dans le Michigan plusieurs fois par an, car le voyage en vaut la peine. Si j'ai des difficultés, je donne généralement à ANCA des outils que peu de gens fabriquent, et nous nous asseyons ensemble pour les concevoir. Ou bien ils m'appellent et nous le faisons par téléphone. En l'espace d'un jour ou deux, nous aurons un outil ensemble. Et ils ne demandent rien pour cela. Ils veulent juste savoir comment ça se passe. Ils nous ont beaucoup aidés".
Pierre a fait une découverte surprenante : il a pu éliminer le besoin de revêtement sur un grand nombre de ses outils en affûtant l'arête de coupe dans une machine de finition de traînée OTEC. "Nos outils durent plus longtemps lorsqu'ils sont affûtés que lorsqu'ils sont revêtus", observe M. St-Pierre. "Nous revêtons un grand nombre de nos outils s'ils sont utilisés pour l'usinage à haute température. Mais nous fabriquons beaucoup de billes coniques pour le titane et nous avons effectué de nombreux tests. Il suffit de préparer l'outil à l'arête pour qu'il dure. Parfois, nous avons obtenu une durée de vie quatre fois supérieure à celle des outils précédents".
Outre les performances accrues, ajoute M. St-Pierre, la préparation des arêtes permet également d'éliminer le délai d'environ une semaine nécessaire pour le revêtement, ainsi que le coût et les frais d'expédition et de manutention supplémentaires. "Une rectification peut coûter 5 dollars ou 100 dollars", poursuit-il. "Mais s'il s'agit d'une rectification à 5 dollars, le revêtement coûtera toujours 10 dollars. Le coût de l'outil est donc multiplié par trois. Nous pouvons éliminer cela avec un processus qui prend quelques secondes". (Le temps de rodage moyen de GKN est d'environ une minute, et l'OTEC traite 25 outils à la fois, selon St-Pierre).
Un centre de profit indépendant
L'atelier d'outillage de St-Pierre est rattaché à l'usine de moteurs aéronautiques de GKN à Newington, au Connecticut, mais il est géré comme un centre de profit distinct. Elle dessert les sept sites de GKN Aerospace Engine en Amérique du Nord et vend des outils à d'autres entreprises aérospatiales locales. Elle a même réussi à faire travailler d'autres entreprises à l'extérieur pour augmenter ses revenus. Il s'agit d'une activité secondaire pour GKN, mais cela vaut la peine d'envisager cette possibilité lorsque l'on décide de procéder à l'affûtage des outils en interne.
Choisir la bonne affûteuse...
Si vous êtes prêt à vous lancer dans l'affûtage d'outils, la question la plus importante est de savoir dans quelle affûteuse vous devez investir. Naturellement, la facilité d'utilisation et l'assistance sont des facteurs clés, et il est judicieux de ne pas se limiter au constructeur de la machine. Demandez à vos fournisseurs actuels quelles machines ils utilisent et s'ils sont prêts à partager des programmes ou à offrir d'autres formes d'assistance. Pour GKN, le choix d'ANCA était évident, car l'entreprise est leader sur le marché et le site suédois dispose de machines ANCA.
"De cette façon, nous pouvons nous entraider", explique M. St-Pierre. "S'ils ont besoin que nous fabriquions des outils, ils peuvent nous envoyer un programme, nous pouvons exécuter les outils, les renvoyer et les outils sont exactement comme s'ils avaient été fabriqués sur place.
Il convient de souligner que, bien que M. St-Pierre ait eu des années d'expérience en matière de fabrication et de résolution de problèmes lorsqu'il a lancé le projet chez GKN, il n'avait jamais affûté d'outil. Il en va de même pour tous ceux qui ont rejoint l'équipe par la suite. "J'ai embauché des personnes dont je savais qu'elles avaient un penchant pour la mécanique, qu'elles comprenaient le monde réel et qu'elles savaient qu'il ne fallait pas trop compliquer les choses", raconte M. St-Pierre. "Ils étaient tous nerveux au début, mais la première chose que nous avons faite a été de nous rendre dans le Michigan pour deux semaines d'entraînement avec l'ANCA. Puis nous avons commencé à courir". Depuis, ils n'ont cessé d'apprendre et ont commis quelques erreurs, ajoute-t-il. Mais ils n'ont envoyé qu'une seule fois un outil qui n'a pas fonctionné.
M. St. Pierre ne tarit pas d'éloges sur le logiciel de l'ANCA : "Tous leurs outils, qu'il s'agisse de recalibrage, de remise en service, de réapprentissage d'une position lorsque vous faites de l'automatisation, vous guident vraiment tout au long du processus. C'est la machine la plus conviviale que j'aie jamais utilisée. Je peux prendre quelqu'un de l'atelier qui n'a jamais vu la machine et il peut fabriquer un outil en une demi-heure. Il peut en concevoir un sur la machine et l'affûter sans savoir ce qu'il fait".
...Et la bonne machine à mesurer
L'équipement d'inspection est sans doute la deuxième décision d'investissement la plus importante pour une salle d'outils, en particulier pour une entreprise du secteur aérospatial. ZOLLER, basé à Ann Arbor, MI, était une autre solution naturelle. Tout d'abord, GKN possédait déjà des prérégleurs ZOLLER, et St. Pierre a apprécié la relation de travail harmonieuse qu'ils avaient établie. Deuxièmement, ZOLLER entretient un partenariat étroit avec ANCA, ce qui se traduit par des solutions qui rendent les deux machines plus performantes. GKN a donc opté pour un ZOLLER "titan" haut de gamme, qui peut mesurer automatiquement chaque attribut de l'outil par voie optique, y compris la forme de la goujure et la préparation de l'arête.
Automatisation avec une grande précision
GKN a choisi d'ajouter des chargeurs robotisés à toutes ses meuleuses d'outils ANCA MX7, ainsi qu'un dispositif de dressage et de mesure interne des meules. Les machines sont également équipées d'un laser intégré qui peut scanner le profil d'un outil et compenser automatiquement le programme d'affûtage pour corriger tout écart par rapport à la forme nominale. Ces caractéristiques se combinent pour permettre aux machines de produire des outils à tolérance serrée tout au long d'une équipe sans personnel. "Nous nous imposons des tolérances de plus rien et de moins un demi-kilomètre sur nos outils", explique M. St-Pierre. Pierre. "Et une tolérance plus serrée pour certains outils. S'il s'agit d'un nez de bille pour l'usinage de finition, nous nous en tenons à quelques dixièmes.
Le "titan" ZOLLER est également équipé d'un chargeur robotisé, que ZOLLER appelle "roboSet2". De plus, les quatre rectifieuses et la machine de mesure peuvent changer automatiquement le diamètre de l'outil pendant les opérations d'extinction des feux. C'est important, explique M. St. Pierre, car l'entreprise fabrique "400 numéros de pièces différents pour GKN. Nous ne fabriquons pas des lots de 1 000 pièces, mais des lots de 15 à 20 pièces". Et à quelques rares exceptions près, ils doivent inspecter entre 10 et 100 % de tous leurs outils. Il est donc essentiel de disposer d'un système de serrage flexible pour éviter les goulots d'étranglement.
Les deux systèmes utilisent des mandrins hydrauliques Schunk qui serrent différents diamètres en insérant une douille intermédiaire. Dans le cas de GKN, un robot remplace la douille. Comme l'a illustré M. St-Pierre : "Le roboSet [ou le chargeur MX7] a déjà tous les manchons à l'intérieur et sait où ils se trouvent. Disons que le lot numéro un est un outil d'un demi-pouce. Le robot saisira la douille d'un demi-pouce et la chargera dans le mandrin. Ensuite, il exécute tous les outils d'un demi-pouce et établit les rapports nécessaires. Une fois cette opération terminée, il changera de manchon, saisira l'outil de la taille suivante et commencera à exécuter le programme. Il vous suffit d'écrire le programme et de sélectionner votre horaire". GKN a personnalisé ses palettes pour qu'elles puissent contenir 5 tailles différentes et M. St. Pierre a déclaré qu'ils pouvaient faire passer 20 conceptions d'outils différentes par le ZOLLER en une seule période de travail sans personnel.
GKN utilise le logiciel d'outillage ANCA pour produire des impressions très détaillées de ses outils, "au lieu des solides fictifs auxquels l'industrie est habituée", comme le dit St-Pierre. "Nous sommes donc en mesure d'inclure tous les paramètres de l'outil physique réel et de la manière dont il est conçu. Ces empreintes dictent ensuite la routine d'inspection. "Sur un outil standard, nous passons en revue 22 à 30 paramètres différents... Mais nous fabriquons beaucoup d'outils à index et à hélice variables, si bien que nous devons vérifier chaque goujure, en particulier sur un montage". Pierre ajoute qu'une inspection complète et détaillée "peut prendre dix minutes, mais il est possible de personnaliser ces programmes et de vérifier en moins d'une minute" un sous-ensemble de caractéristiques spécifiques.
En savoir plus sur le partenariat ANCA-ZOLLER
Pour répondre aux exigences en matière de contrôle qualité, GKN a besoin d'une machine de mesure autonome du calibre du "titan". Mais remarquez que les capacités de mesure de l'ANCA se superposent à celles du ZOLLER. Comment répartiriez-vous les tâches qu'elles peuvent toutes deux accomplir ? Les machines peuvent-elles coopérer ? Pour St-Pierre, l'objectif est non seulement d'obtenir la qualité d'outil requise, mais aussi de maximiser la productivité. Ainsi, par exemple, si un opérateur est disponible, il préfère utiliser la machine "titan" pour scanner un profil d'outil et envoyer les données de compensation nécessaires à la rectifieuse, plutôt que d'utiliser le laser interne de l'ANCA. Cela permet de conserver les outils de meulage de la MX.
M. St. Pierre a également évoqué des situations dans lesquelles l'opérateur n'est pas sûr de savoir comment effectuer un réglage. "Nous utilisons le ZOLLER pour effectuer la mesure et la renvoyer au programme de meulage pour effectuer les corrections. C'est bien qu'ils puissent se parler assez facilement, et ce n'était pas trop difficile à mettre en place... Nous l'avons utilisé sur des outils plus avancés où il y a tellement de paramètres qu'une chose peut affecter l'autre. Nous avons donc laissé le ZOLLER nous aider dans ces cas-là".
GKN commence également à utiliser le ZOLLER pour mesurer les meules, ce qui permet de maximiser la productivité de la MX. "Nous recevons l'équipement nécessaire pour configurer le ZOLLER afin qu'il effectue toutes les mesures des meules, ce qui nous permet de configurer un lot entier et de rationaliser les données dans les rectifieuses", explique M. St-Pierre.
GKN dispose également d'une machine à dresser les roues autonome pour conditionner les roues hors ligne. Mais comme nous l'avons déjà mentionné, si l'équipe est sans personnel, les machines MX peuvent à la fois rectifier et mesurer les outils en cours de fabrication, mesurer et dresser les meules. Pendant ce temps, le ZOLLER effectue l'inspection des outils finis sur les outils précédemment affûtés.
Autres équipements auxiliaires
Tout atelier d'affûtage d'outils a également besoin d'une filtration du liquide de refroidissement et d'un contrôle de la température, ce qui, chez GKN, est assuré par des systèmes Transor à double cuve. Les machines à tronçonner sont également utiles pour dimensionner les ébauches en carbure. Ici, GKN a adopté une approche créative et opté pour une machine d'électroérosion à fil Makino U6. Comme l'explique M. St-Pierre, "la différence de prix n'était pas assez importante pour justifier une telle dépense pour une machine qui ne peut que découper. Nous avons donc acheté une machine d'électroérosion à fil pour réaliser des découpes personnalisées en grandes séries. Nous fabriquons également nos propres fixations et jauges d'inspection pour l'ensemble de l'entreprise. Cette machine s'est amortie dès la première année en fabriquant des pièces qui ne sont pas liées aux outils de meulage". M. St. Pierre ajoute qu'ils utiliseront également l'électroérosion pour découper des profils d'outils, puis rectifier la goujure et le diamètre extérieur dans les ANCA. "Nous pouvons maintenir des tolérances de rectification sur notre EDM. L'entreprise l'utilise déjà pour fabriquer des douilles en steadyrest pour les ANCA.
Ajoutez le logiciel de gestion d'outils TMS de ZOLLER, une imprimante 3D pour les pinces de robot et d'autres outils, une tour de stockage Modula VLM et un marqueur laser, et vous verrez que la salle d'outils de GKN est aussi autosuffisante qu'efficace.
Cela a représenté "beaucoup de travail" et un gros investissement. Mais comme le résume M. St-Pierre : "Personne ne considère ce projet comme un mauvais investissement. Tout le monde dit qu'il aurait aimé que nous le fassions plus tôt".
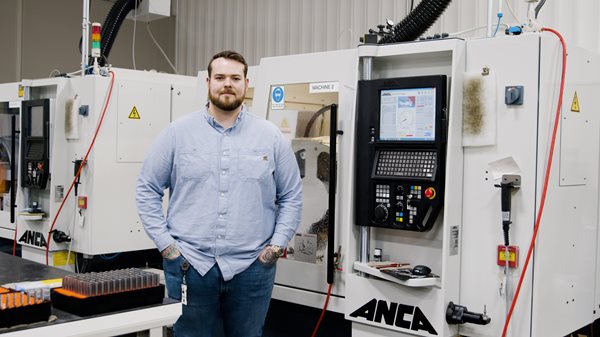
Jeremy St. Pierre a dirigé la création d'une opération d'affûtage d'outils en interne chez GKN Aerospace Engine, qui a été rentabilisée en seulement deux ans (Image fournie par ZOLLER).
6 mars 2024