Biuletyn Sharp E
Wrzesień 2020
Kompleksowe rozwiązanie programowo-sprzętowe ANCA w zakresie łuszczenia kół zębatych
Menadżer Produktu Xiaoyu Wang – Obróbka przekładni
ANCA CNC Machines
Wzrost zapotrzebowania
Prognozy branżowe i badania dotyczące światowego popytu na koła zębate przewidywały wystąpienie do 2019 r. rocznego wzrostu w wielkości 6%, tj. do 221 mld dolarów amerykańskich. Same koła dla pojazdów silnikowych stanowią 45% rynku [3]. Oczekuje się, że elektryfikacja pojazdów będzie miała istotny wpływ na przemysł przekładniowy. W konwencjonalnym układzie napędowym występuje od 25 do 30 kół zębatych. Zamiast 9-10 poziomów przełożeń, silniki elektryczne posiadają prostszy układ przeniesienia napędu z jednym lub dwoma biegami.
Wysokie prędkości obrotowe silników pojazdów elektrycznych, wynoszące nawet do 20.000 obr/min, powodują, że koła zębate w przekładniach muszą być wykonywane zgodnie z jeszcze bardziej ścisłymi tolerancjami geometrii. W nowych konstrukcjach układów napędowych dominują koła zębate wewnętrzne w przekładniach planetarnych. Aby poprawić dokładność oraz wydajność procesu produkcyjnego, branża przekładniowa coraz częściej rozważa wdrożenie technologii łuszczenia. Technologia łuszczenia kół zębatych to rewolucja w produkcji kół zębatych zapewniająca 6 do 8-krotnie większą sprawność niż dłutowanie, większą elastyczność niż przeciąganie oraz umożliwiająca wytwarzanie kół zębatych zarówno wewnętrznych, jak i zewnętrznych [4]. Rosnąca popularność tej technologii spowodowała wzrost zapotrzebowania na frezy do łuszczenia. Lecz w branży obecnie typowe są czasy realizacji do 20 tygodni, co powoduje, że frezy stanowią wąskie gardło w procesie powszechnego wdrożenia łuszczenia.
Konstrukcja frezu do łuszczenia kół zębatych
Podstawą przy konstruowaniu frezów do łuszczenia są szczegółowe i złożone obliczenia geometryczne. Najważniejsza jest kinematyka łuszczenia, która stanowi fundamentalną różnicę między frezami do łuszczenia a tradycyjnymi frezami do strugania.
Kinematyka łuszczenia
Pierwszy proces łuszczenia został opracowany i opatentowany w 1910 r. przez Wilhelma von Pittlera [2]. Kinematyka łuszczenia łączy w sobie ruch toczenia i frezowania, co wymaga synchronizacji frezu i detalu z dużą prędkością. Od lat 60-tych do 90-tych podejmowano wiele prób budowy łuszczarki o wymaganej synchronizacji i zwartości. Jednak dopiero w ciągu ostatnich 10-15 lat pojawiły się maszyny, które uczyniły łuszczenie rozwiązaniem możliwym do wdrożenia w praktyce.
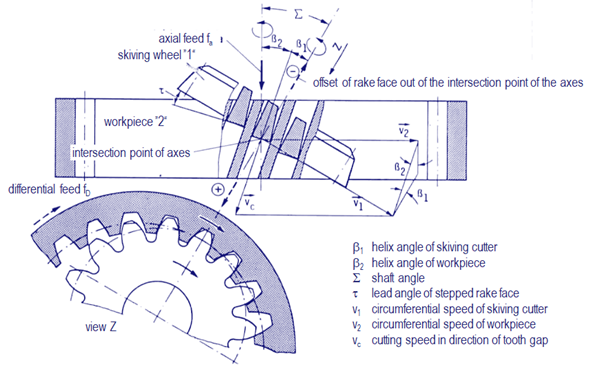
Rysunek 1. Kinematyka łuszczenia. Źródło: König, Fertigungsverfahren Band 1
Frez łuszczący kontra frez strugający
Frez łuszczący to frez typu dłutakowego do kół zębatych, który wygląda bardzo podobnie do konwencjonalnych frezów strugających. Patrząc na relatywny ruch pomiędzy kołem zębatym (detalem) a frezem stwierdzić można, że zasada działania frezu strugającego opiera się na parze kół zębatych o osiach ustawionych równolegle. Frezy łuszczące oparte są natomiast na parze kół zębatych o osiach ustawionych poprzecznie. Para kół zębatych o osiach ustawionych poprzecznie styka się tylko w jednym punkcie, przez co profil i geometria frezu łuszczącego jest bardziej złożona niż w przypadku frezu strugającego. Poza profilem obrabianego detalu, określenie geometrii frezu łuszczącego wymaga znajomości kinematyki: odległości środkowej i okręgów tocznych w zależności od przełożenia przekładni, kąta trzonu i kąta pochylenia.
Zgodnie z zasadami określonymi w normie DIN 1829, krawędź tnąca frezu łuszczącego może być rozpatrywana w kategoriach koła zębatego, które odpowiada kołu praktycznie cylindrycznemu. W przypadku frezów łuszczących profil koła nie jest idealnie spiralny, w przeciwieństwie do frezów strugających.
Wymagana dokładność
Frezy do łuszczenia są klasyfikowane jako frezy typu dłutakowego, w związku z czym obecnie nie istnieją specjalne normy branżowe ich dotyczące. Branża przyjęła powszechnie normę DIN 1829 - część 2 jako domyślną normę pomiarową. Norma DIN 1829 - część 2 określa cechy podlegające ocenie oraz tolerancję stosowaną przy kwalifikowaniu do poszczególnych klas jakości. Na przykład, dla frezów o średnicy referencyjnej mniejszej niż 50 mm i rozmiarze modułu mniejszym niż 1 mm, wymagany błąd formy ff musi być mniejszy lub równy 2 mikronom, aby zakwalifikować się do klasy AA wg DIN.
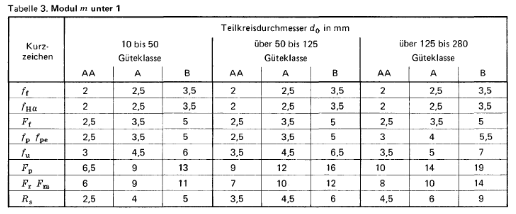
Rysunek 2. Tabela 3 - norma pomiarowa Źródło: DIN 1829 - część 2
Ze względu na fakt, iż frezy łuszczące są nowością, wiele wzorcowych maszyn pomiarowych w branży nie posiada modeli matematycznych do pomiaru profilu frezu, co stanowi szczególne wyzwanie w procesie produkcji i kontroli jakości.
Technologia łuszczenia według ANCA
Odpowiadając na potrzeby rynku, ANCA opracowała kompleksowe rozwiązanie programowe i sprzętowe, zapewniające prawidłowe zaprojektowanie i zoptymalizowanie frezu w wydajny sposób. Zaprezentowana po raz pierwszy na EMO w Hanowerze w 2019 roku nowa linia szlifierek GCX Linear wyznacza standardy w produkcji frezów łuszczących. Dzięki wszystkim osiom typu liniowego dla większej precyzji, szlifierka GCX Linear może wykonać wszystkie czynności w jednym cyklu. Posiada ona funkcje specjalnie zaprojektowane do wytwarzania frezów łuszczących i strugających najwyższej klasy jakości AA według normy branżowej DIN.
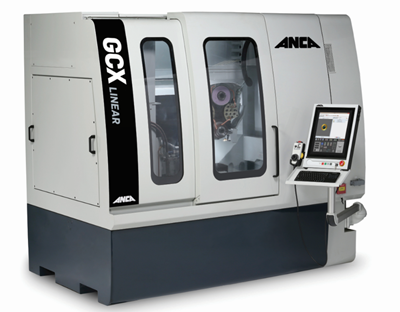
Rysunek 3. Szlifierka ANCA GCX Linear
Kompleksowy pakiet oprogramowania
Pakiet oprogramowania GCX składa się z wielu komponentów służących do produkcji i ostrzenia dłutaków. Umożliwiają one projektowanie, symulację, programowanie sekwencji szlifowania, edytowanie i obciąganie ściernic z obsługą pełnej wirtualizacji procesu wytwarzania narzędzi, co pozwala zmniejszyć czas przygotowywania oraz redukuje braki.
Narzędzia do skrawania kół zębatych, takie jak frezy łuszczące i strugające, cechuje skomplikowana geometria. Proces projektowania polega w dużym stopniu na optymalizacji iteracyjnej. Jest to szczególnie ważne w warunkach skrajnych, jak w przypadku kolizji między elementami. Na stanowisku projektowym frez może być opracowany na bazie podstawowych danych o kole zębatym. Oprogramowanie pozwala na symulację kinematyki łuszczenia w celu weryfikacji konstrukcji frezu i skorygowania ewentualnych kolizji.
Oprogramowanie iGrind – umożliwia wykonywanie operacji szlifowania obwiedniowego z możliwością tworzenia kąta natarcia o profilu stopniowym i stożkowym, jak również rowkowania, szlifowania na okrągło, edycji geometrii stopniowej i wielu innych operacji. Proces szlifowania można symulować i poddawać analizie w programie CIMulator3D.
Precyzyjne obciąganie ściernic
Obciąganie ściernic o skomplikowanym profilu ma decydujące znaczenie dla osiągnięcia wysokiej dokładności kształtu profilu zęba frezów łuszczących. Wykorzystujący najnowszą technologię monitorowania emisji akustycznej system AEMS jest "uchem" szlifierki GCX Linear, dostrojonym do wysokich dźwięków wytwarzanych przy obciąganiu ściernic. AEMS wyposażony jest w zaawansowany algorytm uczenia maszynowego, który uczy się i nasłuchuje jednocześnie. System może być nauczony wychwytywania odpowiednich dźwięków w celu zapewnienia idealnego obciągnięcia ściernicy nawet w środowisku produkcyjnym o wysokim stężeniu hałasu. Zapewnia to obciąganie profilu ściernicy z dokładnością mikronometryczną w możliwie najkrótszym czasie, przy jednoczesnym minimalnym zmniejszeniu rozmiaru ściernicy.
Poprawiona stabilność termiczna
Dla zapewnienia spełnienia rygorystycznych wymogów dotyczących dokładności, niezmiernie istotna jest stabilność termiczna maszyny. Firma ANCA opracowała technologię kontroli temperatury silnika (MTC, zgłoszona do opatentowania) służącą do aktywnego zarządzania i utrzymywania temperatury napędzanych wrzecion w szlifierce GCX Linear. Oprócz znacznego skrócenia czasu nagrzewania się maszyny, poprawy wydajności i wykorzystania szlifierki, system MTC utrzymuje - co najważniejsze - stałą stabilność termiczną wrzeciona w czasie, niezależnie od zmian obciążenia lub prędkości obrotowej wrzeciona, czy też temperatury płynu chłodzącego wrzeciono. Dzięki temu znacznie zwiększa się powtarzalność wymiaru wytwarzanych detali.
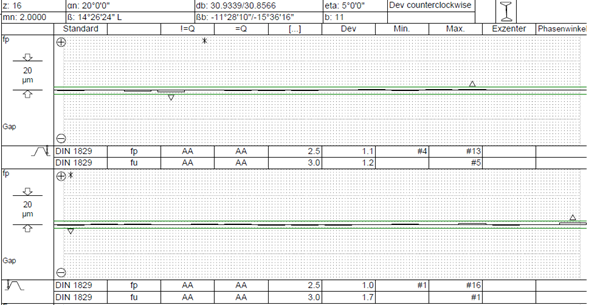
Rysunek 4. Przykładowy raport z pomiaru skoku frezu wyprodukowanego na szlifierce GCX Linear ze zmierzonym indywidualnym błędem skoku fp wynoszącym około 1 µm oraz sąsiadującym błędem skoku fu poniżej 2 µm.
Referencje
- Wilfried König. (n.d.). Fertigungsverfahren Band 1. ISBN 978-3-662-07205-9 - 1997
- Pittler von, W. Verfahren zum Schneiden von Zahnrädern mittels eines zahnrad-artigen, an den Stirnflächen der Zähne mit Schneidkanten versehen-en Schneidwerkzeuges, Patent Application, Germany, March, 1910
.
- World Gears Industry study with Forecasts for 2019 & 2024 The Freedonia Group
- Dr. H.J. Stadtfeld Power Skiving of Cylindrical Gears on Different Machine Platforms, American Gear Manufacturers Association Fall Technical Meeting, 2013
19 sierpnia 2020