ANCA Academy
March 2019
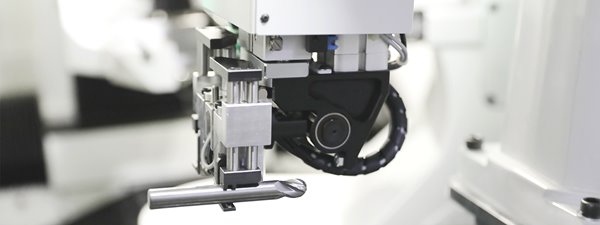
The world of grinding machine technology is hurtling towards automation. Lured by benefits including improved productivity, access to better machine data and the promise of lower production costs, more and more tool manufacturers are choosing to network their machines and control them through cloud-based management suites.
In fact, automation can be applied to every stage of the process, not just your machinery; from customers ordering tools online, to orders being processed through the ERP system, to the dispatch of the products.
A survey by McKinsey showed that in manufacturing around 749 billion hours are worked each year around the world. Of these, about 60% (478 billion hours) were automatable with existing technology.
Imagine what could be possible if even a small number of those 478 billion labor hours were converted to planning, analysis and strategy hours.
It would be the end of employees standing in front of a grinding machine loading programs, manually measuring tools, correcting programs and repeating the process all over again. Instead, the humans would be ‘hands-off’ taking a higher-level view of production instead of being involved in – pardon the pun – the day-to-day grind.
Jumping to automated or semi-automated production is a big leap for many tool manufacturers. However, with cloud technology fast becoming the norm, and every next generation grinding machine able to be easily networked, it’s a leap that all tool manufacturers will need to take to stay competitive.
But in this world of automation can innovation survive? If humans are no longer involved with the machines, will innovation be stifled?
Grinding machine automation doesn’t mean losing innovation.
The short answer is no.
The longer answer is this:
Automation can actually mean more innovation. The automation process triggers curiosity in humans, we’ve seen it first hand. Suddenly people’s eyes are opened to what is really going on with their machines and with their production workflows. They are no longer involved in the nitty gritty of manual processes and their time is freed to look deeper, analyze data and find better ways to do better things.
How to encourage innovation in the age of automation
Innovation requires work. It’s not something that just happens. Here are some tips for optimizing your innovation potential post-automation, using your existing staff or tapping in to new experts in innovation.
Tap into the brain power
Grinding machine automation gives manufacturers the opportunity to better use their human resources. When staff are shifted from in front of the machines to production planning, it can create a cultural shift. No longer are your staff just the do-ers, they are the thinkers. Now, with time, data and real-time visibility over grinding machine production they can actively search out process improvements, and make better tools, faster.
They begin to think outside the box.
Create a brains trust
It is probable however that your skills needs within the business will change. With less hands on the floor you’ll need more hands analyzing data and working on new processes. Data scientists, software engineers, analysists and other technology staff all have a place in the modern factory. These are the innovation experts who can analyze machine insights in the context of market pressures and the capabilities of your machines to deliver you truly innovative improvements.
Let your vendors tap into what you need most
Information sharing also helps vendors design better machines. With access to rich machine and operational data they can really understand what your business is trying to achieve and develop valuable solutions in response. It also means finding that golden nugget of preventative maintenance, where your grinder is connected to the cloud so that the vendor can proactively maintain your machine to achieve zero down time.
Test faster
In the post-automated, ultra-connected factory testing is done virtually. Being able to simulate tooling and modeling not only creates less waste but also speeds up trials by up to 100%. Time that is better spent on reiteration and constant tool improvements.
Two of the biggest benefits of grinding machine automation are time and data. Both of these are essential elements of innovation. The automation of machines is simply the next step in the evolution of manufacturing and with the right skills to hand, the opportunity for innovation has never been better.
18 March 2019